|
|
|
|
|
|
|
|
|
|
|
|
|
|
|
|
|
|
|
|
|
|
|
|
|
|
|
|
|
|
|
|
|
|
|
|
|
|
|
|
|
|
|
|
|
|
|
|
|
|
|
|
|
|
|
|
|
|
|
Ceramic Shells for Direct Casting of Metal Parts
Three Dimensional Printing is the only process that fabricates ceramic molds directly from a computer model with no intervening steps. With 3D Printing, a ceramic shell with integral cores may be fabricated directly from a computer model. This results in a tremendous streamlining of the casting process as compared to the traditional lost-wax casting process (see figure below). Soligen, Inc. has licensed the 3DPTM technology for producing shells, and has helped companies achieve dramatic reductions in turnaround times for metal castings.
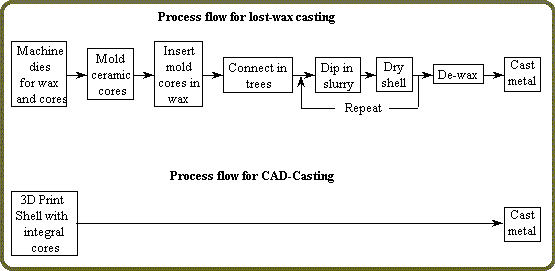
Typically, molds by 3D Printing are fabricated using a refractory powder such as alumina and an inorganic binder material such as colloidal silica. After firing, the loose powder is removed from within the shell resulting in a shell which is similar in composition and properties to those now made in the lost wax process by dipping wax forms in ceramic slurries. However, no part specific tooling is needed 3D Printing has produced metal castings for a wide range of applications including aerospace, medical implants, automotive.
|
|
|
|
|
|
|
|
|
|
|
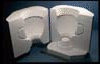 |
|
|
|
|
|
|
|
|
|
|
|
|
|
|
Slip casting mold
|
|
|
|
|
|
|
|
Shorter time, less money
- no need to cut special tooling
- fewer steps
|
|
|
|
|
|
|
Improved tolerances
- fewer patterns transfered
- eliminate "core shift" problem
|
|
|
|
|
New design capabilities
- local control over thermal conductivity
- controls grain structure
- hollow cores permit
- removal of long thin cores
- local control of surface texture
|
|
|
|
|
|
|
|
|
|
|
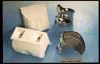 |
|
|
|
|
|
|
|
|
|
|
|
Shell for artificial knee implant
|
|
|
|
|
|
|
|
|
|
|
|
|
|
|
|
|
|
|
|
|
|
|
|
|
|
|
|
|
|
|
|
|
|
|
|
|
|
|
|
|
|
|
|
|
|
|
|
|
|
|
|
|
|
Copyright 1989-2000, 3DPTM Laboratory, MIT
|
|
|