FootStepper: an effort-based locomotion
interface
Abstract
A "footstepping" effort-based
locomotion interface is described. Built around an
inexpensive and readily-available exercise machine,
it provides an effective interface to walk-through
VEs.
Keywords
Effort-based locomotion, locomotion interface,
virtual walk-through.
1 Introduction
The FootStepper was created to solve a practical
need for a method of moving through a large-scale
virtual environment in a more realistic manner than
typical hand control or gesture based interfaces
allow. It is a general problem in interface design
that certain modalities become "overloaded" with
many functions, requiring the user to keep track of
functional modes or complicated codings to achieve
actions that in the real world might require little
thought. In addition to this problem, there is a
tendency to design controls using the prevailing
interface hardware even when this hardware (e.g. a
keyboard or joystick) bears only an abstract
correspondence to the desired action. These
tendencies are understandable given the ubiquity of
keyboards and joysticks, and the ease of
integrating their output into a software system,
but there are clear benefits to expanding the
repertoire of interface devices to more closely
match the capabilities of the human body.
In the present case, it is fairly obvious that,
for most people, the preferred mode of moving about
a large-scale (building sized) space is simple
walking from place to place. A locomotion interface
for a VE walkthrough should take advantage of this
intuitive mode of action. There has been a great
deal of work performed on locomotion interfaces
appropriate to various scales of VE and tuned to
different needs, including work performed at
Sarcos, MERL, Virtual Space, and elsewhere, which
has been summarized
in the literature. Two significant interfaces
worth noting are bicycle-based, for use in outdoor,
very large scale worlds: Ben Brown's Tektrix
bike built for Georgia Tech's virtual
recreation of the Atlanta Bicycle Road Race of the
1996 Olympics, and Mike Benjamin & Thatcher
Ulrich's VR
Bike input device for MERL Diamond Park.
These interfaces are noteworthy because they show
what can be accomplished by combining commercially
available parts (like bicycles) with clever
motorized attachments for simulating the forces
that normally occur when moving through the
world.
In the area of walking interfaces, the seminal
work on the "Virtual Perambulator" (Iwata 1996) is
particularly relevant in that using it requires
effort as well as motion to move, just as is
required in the real world. Relevant research on
imparting constant and inertial forces to cause the
user to expend energy has been carried out at the
University
of Utah using the Sarcos Treadport interface
(Christensen 2000). The possibility of physical
exertion and fatigue when traversing a space is
likely to add to the user's sense of presence by
allowing the physiological state of the user in the
VE to match that of the corresponding experience in
the real world. Thus the user's mental state
and physical state will be appropriate to
the activity in the VE simulation. There may also
be more subtle but important implications to using
effort-based locomotion, involving spatial
apperception, path integration and distance
estimation. These aspects have not yet been
thoroughly studied, but have been topics of
investigation in our laboratory for the past few
years beginning with our "Fingerwalker" system
(Fitch 1998) through the present studies using the
FootStepper.
In designing the FootStepper, three interface
requirements were considered of primary importance;
that the user be able to locomote in a straight
line, turn in place, and reverse direction, all
reliant solely upon the modalities of leg motion
and body attitude. Walking forward using the
FootStepper involves simply pumping the foot pads
of the device symmetrically as one would expect.
Turning in place is achieved by pumping the pads
asymmetrically (as though dragging one foot), and
walking backwards is facilitated by shifting one's
weight to the rear of the foot pads while walking
in the usual fashion. This important latter
activity, with the weight concentrated on the
heels, is strikingly similar to walking backwards
in the real world, particularly when compared with
other toggle methods of selecting "reverse
gear."
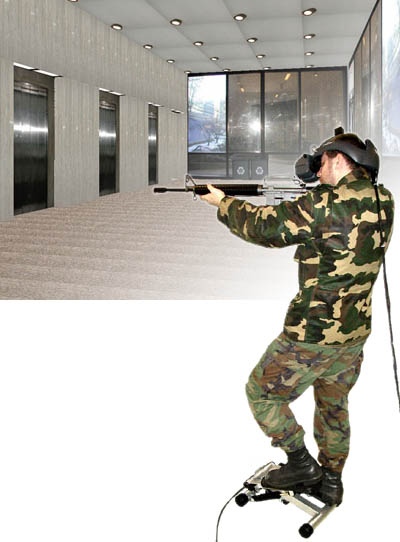
Figure 1. Photograph of the
FootStepper in use in a VE walkthrough of
building-36 at MIT (a bit of impromptu "building
clearing" ).
2 Hardware
The FootStepper is based on a sturdy but
inexpensive (about $100) exercise machine sold at
www.brookstone.com (see figure 2). This unit was
originally selected not only for its robust
construction, but also for the simple adjustment of
step amplitude and the integral dampers that
appeared to be easy to modify. In addition, the
unit includes a magnetic reed switch and magnet
assembly for use by its built-in calorie counter.
Further examination revealed that the reed switch
arrangement was not adequate for our purposes and
subsequently the switch and the built-in factory
electronics were discarded.
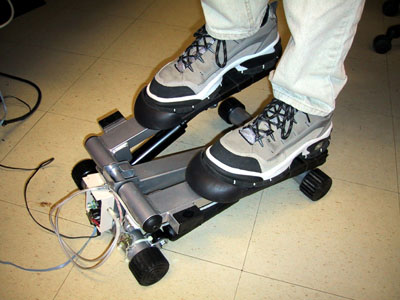
Figure 2. Close-up photograph of
the FootStepper, which is based on an exercise
machine sold at Brookstone (the StepFlex
Compact Fitness Center Mini Stepper,
Brookstone sku#
288209).
The foot pedal position signals are derived from
the action of a magnet (attached to the moving
lever) on a linear Hall-effect sensor. Originally
we used the factory-mounted magnet, but the
position and strength of that magnet were not ideal
at all of the possible step amplitudes that we
wished to measure. Figure 3 shows the alternate
arrangement that we have successfully used. Label
"A" indicates the position of a powerful rare-earth
magnet that we glued to the lever at the pivot
sleeve, label "B" shows the position of the
Hall-effect sensor mounting post (attached to the
stationary base of the machine. The hall-effect
sensor can be obtained directly from Allegro
MicroSystems Inc. Our prototype used a UGN3503LU
having a sensitivity of 1.3mV/Gauss (purchased from
Newark Electronics), however this device has been
superceded by newer models in different (smaller)
packaging, as listed on the Allegro datasheet web
page for the UGN3503
series of Unipolar Ratiometric Linear Hall-Effect
Sensors. The Neodymium magnet
(CR30812-37) was obtained from Edmund
Scientific.
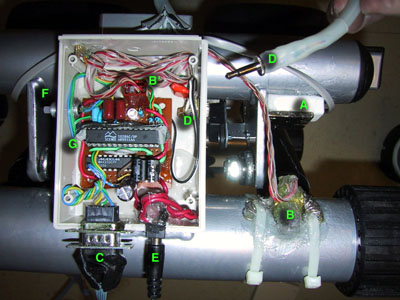
Figure 3. Photograph of control
circuit and sensors. A: magnet, B: Hall-effect
sensor, C: D9 serial interface connector, D&D':
plug & jack for heel sensor, E: power input, F:
reset pushbutton, G: IC's (Ubicom SX28
microcontroller & Maxim MAX233 RS232
buffer).
The amount of effort required to perform each
step on the unmodified machine turned out to be too
great regardless of the adjustment of the amplitude
control. To put the level of effort within a useful
range for sustained walking, we considered removing
the dampers completely. However, some amount of
controlled resistance was desired in order to
simulate the energy expenditure of walking as well
as to assist in balancing while standing on the
device. To modify the dampers we simply drilled two
3/16" holes near the end of each cylinder, as shown
by the green arrows in figure 4. This operation was
slightly messy since the damper is filled with
silicone liquid, which we extracted by pumping the
damper repeatedly until empty. A future enhancement
to the system will be to add
electronically-controlled valves to the damper in
order to vary the damping factor under computer
control (to simulate walking on hilly terrain).
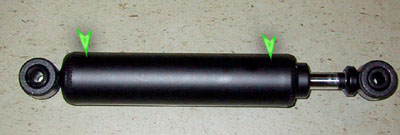
Figure 4. Photograph of damper
piston. The arrows show location of drilled vent
holes.
The heel pressure sensor is shown in figure 5.
The purpose of this sensor is to enable the
software to determine when the user is walking
backwards. This condition is detected when the user
maintains higher than normal pressure on the heels
while stepping. We are not totally convinced that
this method feels as natural as we would like, but
it is a workable solution until something better is
developed. The pressure sensor was constructed
using Xilor
Inc. Zoflex ZF series pressure-sensitive
conductive rubber sandwiched between a pair of
aluminum sheets. We found it difficult to attach
the conductive rubber to any material, so our
method was to confine it from sliding around using
cloth tape, then relied on the fact that it is not
subject to any sheer or sliding forces. We have not
noticed any sliding problems with this method, and
upon removing the covering to take the photograph
we discovered that the Zoflex material was still in
the original configuration.
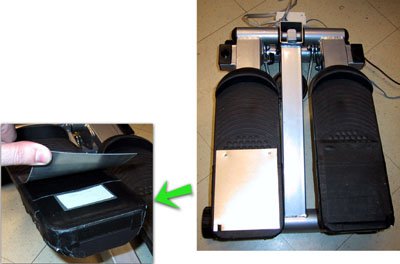
Figure 5. Photograph with detail of
heel pressure sensor construction.
A microcontroller and associated electronics are
used to convert the analog signals from the step
and heel sensors into serial data that can be
accessed through a com port. Figure 6 shows the
schematic of this circuit. The analog-to-digital
conversion is performed in software based on the
charge/discharge timing of the R/C networks
attached to the C4 thru C7 pins. A dual-color
common cathode LED was wired to pins B5 & B6 to
allow for feedback to the user. Pins A1 and A2
provide serial I/O via the MAX233 buffer/converter
chip. A three-terminal 50MHz resonator available
from Parallax.(#250-15060
or #250-05060)
was used to complete the clock oscillator circuit.
The assembly code for programming the SX28
microcontroller is listed in the appendix. The
software serves as a "software UART" for generating
and receiving the serial I/O signals, does the
timing and control to effect the analog-to-digital
conversion, and also performs some built-in
statistical calculations such as step amplitude,
skew, and timing. Some of these latter features
were not used (or were redundant) in our final VE
walkthrough described in the next section, but were
left in the listing because having these features
"built into the interface" could be useful in other
contexts. The code listing includes comments
describing the protocol by which the host makes
requests for status and statistics information
(especially position of step and heel
pressure).

Figure 6. Schematic diagram of
controller, including serial interface and sensors
(click to enlarge
image).
3 Software
The software used to interface the FootStepper
to a virtual environment walkthrough was written in
C for Windows NT. The walkthrough itself was
generated using the Vega realtime simulation
software from Multigen-Paradigm,
Inc. As Windows NT is a relatively common
platform for simulation, no attempt has been made
to remove Windows-specific references in this
section; however as Vega is a proprietary
third-party API, Vega-specific code has been
replaced with generic descriptions.
The FootStepper software is separated into three
modules: the serial communications drivers, a
generic "motion model" for the user's viewpoint,
and a dedicated FootStepper querying and processing
engine. The communications module is typical of any
that would be used to receive information from a
motion tracker or other serial device, and is
included in the Appendix primarily for the aid of
other Windows NT users.
The motion model is a thread that runs
synchronously with the rendering engine. Before
each frame is rendered, the motion model is queried
for an update to the user's position. Once the
user's viewpoint is updated, control is passed to
the rendering system which generates the frustum
and draws the scene. As this process is independent
of the specific nature of events, such as
locomotion, affecting the user's position, the
motion model was implemented in a generic fashion
such that it relies on only two input variables,
the rate of linear motion (forward or backward) and
the amount of rotational motion (turning left or
right). This also renders the motion model immune
to adjustments to FootStepper processing
algorithms, and allows the possibility of
on-the-fly selection of alternative ground-based
locomotion schemes. The two input quantities are
global variables protected by a mutex (mutual
exclusion semaphore). The exact values of the
variables are relative to a pair of constant base
moving and turning velocities. As the motion model
code is highly Vega-specific, a pseudocode
description of the entire update query procedure is
presented as follows:
Pre-frame update:
Wait for stepper variable mutex
Copy global step and skew variables into local variables:
step_apply = step;
skew_apply = skew;
Release stepper variable mutex
Subtract gravitational descent from vertical position:
user_z = user_z - gravity;
Compute new heading based on skew variable and time since last frame:
user_heading = user_heading - (turn_speed * skew_apply * dt);
Compute new position based on new heading, step variable and frame time:
user_x = user_x - (base_velocity * directional_sine * step_apply * dt);
user_y = user_y + (base_velocity * directional_cosine * step_apply * dt);
Query collision detection intersectors
Readjust user position based on collision information
Return
The FootStepper-specific processing is performed
in a separate thread that runs asynchronously other
than accepting and releasing the mutex once per
cycle to ensure that minimal delay is imparted to
the motion model. Each cycle, the thread queries
the FootStepper for the most recent local maximum
and minimum foot positions, the current position,
and the status of the backwards attitude sensor.
From these values the most recent step amplitude is
calculated as the difference between the maximum
and minimum positions, while the skew is calculated
as their average. If the foot position is within
five percent of the appropriate maximum or minimum
(depending on whether a right or left footfall is
being recorded), then a step is registered. It
should be noted that this generates a step having
the previous step amplitude; this was considered
acceptable in order to enable the user to take
single steps, which was identified as an important
form of small-scale maneuvering. If the true local
maximum or minimum were to be insisted upon, in
order to register a completed step the user would
have to generate a physical inflection
corresponding to the beginning of a second step. In
any case, the perceived difference between real and
virtual step sizes over a single step seems small
at worst.
If a step is recorded on the current cycle, the
procedure determines whether it is a walking or
turning step, according to the value of the skew.
If a walking step, the value of the back attitude
sensor is compared with a threshold and the step
amplitude negated if it is determined to be a
reverse step. The step amplitude is then fed into
the appropriate accumulator to adjust the current
step rate or turn speed. A decelerator also
provides negative feedback to each accumulator, to
rapidly bring the user to a halt when stepping
ceases. If the position value has been updated over
the past cycle, even if a step has not been
recorded, the decelerators are temporarily disabled
to smoothen the velocity during continuous walking.
A complete listing of the FootStepper processing
code is included in the Appendix.
The FootStepper software currently supports only
linear motion and turning in place as priority was
given to preventing the registering of undesired
turns, in order to make the interface as robust as
possible for novice users, especially given the
added task of maintaining balance while wearing an
HMD. In addition, it is clear from the description
above that there is an important latency present in
the interface. Some latency is inevitable in any
virtual environment locomotion interface, as the
device must spend time recording and interpreting
users' movements in the real world before updating
their virtual location and scene view. The
principal latency inherent in the FootStepper is
that no update to the user's velocity and hence
perception of motion is initiated until the first
complete step has been recorded. This was necessary
due to the use of a single modality for both
position and orientation control -- during the
first moments of a step, the system has no way of
determining whether the step is symmetric or
asymmetric, and thus whether the user intends to
move or turn. This latency does not seem overly
distracting, and the reduced amount of cognitive
overhead and coordination required through the
reliance on a single modality led us to consider
this trade-off acceptable.
Acknowledgements
This work was performed with support from ONR
grants N00014-96-1-0379 and
N00014-01-1-0062.
References
Christensen, R., Hollerbach,
J.M., Xu, Y., and Meek, S. (2000). "Inertial force
feedback for the Treadport locomotion interface."
Presence: Teleoperators and Virtual
Environments, Vol. 9, No.1, pp. 1-14.
Fitch, S.B. (1998). The
Finger Walker: A Method to Navigate Virtual
Environments. M.Eng. Thesis supported by ONR
grant N00014-96-1-0937. Cambridge: Massachusetts
Institute of Technology.
Iwata, H., & Fujii, T.
(1996). "Virtual Perambulator: A Novel Interface
Device for Locomotion in Virtual Environment."
IEEE Proceedings of VRAIS'96, pp. 60-65.
Appendix
Code listing for Ubicom SX28 micontroller
(click here).
Serial code listing (click
here).
Step monitor thread code listing (click
here).
|