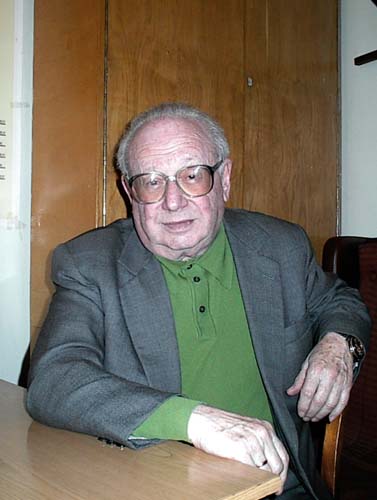
|
Interview with Georgii Priss
Moscow, May 23, 2002
Georgii Moiseevich Priss was born on July 11, 1925. In 1948 he
graduated from the Moscow Aviation Institute
and joined the Scientific Research Institute No. 885 (NII-885), which
designed control systems for rocketry. In 1963 NII-885 was divided into
two institutes, led by the Chief Designer of radio control systems
Mikhail Ryazanskiy and by the Chief Designer of autonomous control
systems Nikolay Pilyugin. Priss joined Pilyugin’s Scientific-Research
Institute for Automation and Instrument Building (NII AP). In 1992, the
Institute and its experimental factory formed the
Research-and-Production Association of Automation and Instrument
Building (NPO AP). In 2001 the Association was reorganized into the
Pilyugin
Research-and-Production Center for Automation and Instrument Building
(NPTs AP). Georgiy Priss worked on gyroscopic equipment for the first
Soviet rockets and served as the principal integration engineer during
the design of control systems for the R-5 and the R-7 rockets. In 1956
he became Pilyugin’s deputy in charge of equipment and the
test-and-launch complex. Priss was the principal developer of control
systems for the N1 and the Buran projects. Currently he is the head of
the Integration Department at the Pilyugin Center.
This interview was conducted and translated from the Russian by Slava
Gerovitch. This interview was published in the collection: Slava Gerovitch, Voices of the Soviet Space Program: Cosmonauts, Soldiers, and Engineers Who Took the USSR into Space (Palgrave Macmillan, 2014).
|
Gerovitch: Could you tell me about yourself: when did you join
Pilyugin's firm, what did you work on?
Priss: I joined the firm in January 1948. The firm was
organized by the well-known order of May 13, 1946, signed by Stalin. It was
a general order to start the development of rocket weaponry. It
contained specific assignments to various ministries. For example, it
would read "on the basis of such-and-such factory, create an
organization that will be doing this and that." A similar
assignment was given to the Ministry of Electrical Industry, in which
there was a factory that produced communications equipment: telephone sets, telephone
exchange switchboards, and so forth; it was located on Aviamotornaya. On the basis of
that factory, our organization was created. It had two assignments: the creation of
autonomous control systems and the creation of radio control systems. Therefore, there were two
chief designers in our organization: Nikolay Alekseevich Pilyugin and Mikhail Sergeevich Ryazansky. Pilyugin was the
chief designer of autonomous systems, and Ryazansky worked on radio
systems. All of them - Pilyugin, Korolev, [Valentin] Glushko - in 1945, after the Victory, were
sent to Germany, where they studied captured rocket technology. There were
doubts and debates in the Soviet Union: whom to assign the production of
rocket technology? The Air Force refused; the Ministry of
Ammunition also refused. In the end Nikolai Dmitrievich Ustinov understood
the value of this technology - he was then the Minister of Defense
Industry - and he took up this job. Then Stalin's order appeared, and
all ministries received specific assignments.
The people who had worked at that factory now switched to rocket
engineering. They were telephony specialists evacuated from Leningrad, from
the Krasnaya Zarya factory. They were very competent in their work. They
were inventors, who in the early days of telephone engineering were engaged in
the construction of telephone systems - not only telephone sets, but also stations. The
captured German rocket technology was based on relay circuits. Analog
control devices used vacuum tubes. There were also some
gyroscopic devices. The Germans had only five [control] devices in total.
Pilyugin, who had studied this technology in Germany, was appointed to supervise
these relay specialists. He had graduated from the Moscow Advanced
Engineering School (MVTU). In 1947, when we came, he had about 70
people. Back in 1946 he had just 30. In 1947 Pilyugin was a member of
the graduation examining board at the Moscow Aviation Institute. He
attended graduation project defenses and listened to the presentations.
He used the following trick: he talked not to the students who came to
defend their own projects but to those who came to listen to other
students' presentations. They were
about to defend their own projects, and they came just to listen. Based
on their projects, Pilyugin selected the first group of six
students and hired them.
I was in the second group. I met Pilyugin at the end of December
1947, when he attended project defenses of the first group. We still had
about six months left to do our own projects. He told us: "Come to me,
and do your projects with me." Because of secrecy restrictions, he did
not tell us any details about his work, but just said: "Here are such and such
research topics. If you want, I can hire you as technicians while you do
your projects." We did not know any specifics. We thought, why not? What's
the difference where to do our projects? So we agreed. We came to do our
projects in January, defended in June-July 1948, and all stayed with him. There was also the third group, in 1950-1951. Stalin's order was
all-inclusive: it had a provision for the organization of special
student training and student job placement in the centers of rocket
industry.
Pilyugin assigned topics by intuition, as I understand, and I got
integration. There were six of us, and the majority began working on
specific devices, while I was assigned to the integration laboratory. I
defended my project, and since then I have been working on integration.
The Soviet rocket industry had a unique organizational structure. If you
take aviation industry, you won't find there a "chief
designer" of the control system for a particular aircraft. There is
no such position, even though there are control systems, and they also
have gyroscopic devices and computing devices, and their tasks are as
complex as ours, and maybe even more. In aviation industry, the chief
aircraft designers - Aleksandr Yakovlev or Andrei Tupolev - used the
compilation method. They always had "equipment groups." Many
of our college mates, who graduated the same year, before, or after, were
placed in so-called "equipment brigades." They visited various aviation firms that produced autopilots, electric
transformers, radio equipment, and so on, and searched for the equipment
they needed. At best they could order equipment, but usually they had to
take whatever they were given, and then they assembled these pieces and created a control system.
By contrast, in the rocket industry the chief designer of [autonomous] control systems
[Pilyugin] was appointed at the very beginning. Next to him was the
chief designer of gyroscopic devices, Viktor Ivanovich Kuznetsov. The
chief designer of radio control systems also was appointed. The Council of Chief
Designers was created. It also included Sergei Pavlovich Korolev, the
engine designer Valentin Petrovich Glushko, and the ground complex designer
Vladimir Pavlovich Barmin. That's six people in total, the entire Council. They resolved all
the technical questions.
What is integration? All these individual devices must be put together to make
a unified cyclogram; there must be some equipment that would integrate
everything. For example, we needed to integrate various parts of the
power system: an accumulator battery and various converters into other
kinds of energy (gyroscopes, for instance, require alternating current).
We needed to prepare a cyclogram of the pre-launch sequence, to operate
the engines and all onboard systems, and so on. It is the control system
that turns on the engines at lift-off.
I graduated from the Equipment Faculty of the Moscow Aviation Institute.
This Institute is distinguished by its broad education. They taught us
how to design oxygen equipment, hydraulic equipment, radio equipment,
and other kinds of devices. I was finishing college after the war, and
at that time and during the war lots of new types of equipment appeared
in Russia: American airplanes on lend-lease contracts, captured German
equipment, and alike. We began studying all this. In the Faculty of
Equipment and Instrument Building, the department of Viktor Naumovich
Mil'shtein organized a group to study new equipment during an
additional, eleventh semester. I got into this group. My diploma read
"mechanical engineer with specialization in gyroscopic devices." For me,
the idea of integration was familiar; I knew where every type of
equipment belonged.
Since then, I have been doing integration. I was the lead integration
engineer on the R-7 rocket, and before that on the R-5. I worked also on
the very first rockets, the R-1 and the R-2, but as an ordinary
engineer, not as the lead engineer. I was the lead developer on the N-1
and on Buran. Since 1956, I have been Pilyugin's deputy in charge of equipment and
the test-and-launch complex. Pilyugin since died; his former post is no
longer call the Chief Designer, but the General Designer, and I am still
a
deputy. Now I am the head of the Integration Department. We currently
work on a joint project with Australia on the Aurora space-rocket
system. We have the Integration Division, which includes several
departments. Different departments work on the integration in different
projects. When you finish the integration for one project, you switch to
another. I also work on the problems of stabilization routes (the entire
control system is divided into separate functional routes) and on
communication with radio operators for other projects.
There was a period in the 1960s when I was the head of the entire
Integration Division. In 1963 we moved from Aviamotornaya to the
Southwest district, and after 1963 I was the head of this division and was
working on the UR-500, on the Proton, and on the N-1. Almost 600 people
worked in that division.
Gerovitch: Did you attend any launches?
Priss: Yes, of course. I attended all the launches of the N-1 and
the first, unsuccessful attempt to launch Buran. Then I left for Moscow
and did not return for the second attempt, but stayed at the Mission
Control Center. I was curious to see the operations of the Center. I had
already been to the launch site, and those who see the launch do not see
the landing. Those who sit in the bunker during the launch cannot be at
the landing site. And at the Center
you can see everything and know everything.
Gerovitch: When did the idea of using onboard computers in
spacecraft control systems first arise? Who suggested it first? What
reaction did it provoke? Was it implemented right away?
Priss: By the time this idea emerged, the use of computers had already
been widespread. There already existed ground computing systems; some information
about the construction of specialized computers for guidance (not just
spacecraft guidance) had appeared. Generally speaking, this idea was in
the air. Computers had already spread quite widely. It was abundantly clear,
especially for the main designer of control systems for spacecraft
Nikolai
Alekseevich Pilyugin, that computers could be used for solving problems
of guidance and that they had many advantages over analog systems, which
had been used before. It is hard to tell, to whom the idea of using computers for these
problems came first. This idea was facilitated by the achievements of
engineering at that time, including the achievements in computing. At
the initial stage of the development of computers, it was simply
impossible to use them on board because of the large dimensions and huge energy
consumption, by the mid-1960s technology advanced so much - both in
terms of basic elements and design techniques - that computers became
quite acceptable by these external parameters.
The first onboard computer was installed on a space vehicle sent to
Mars. It was part of the control system for a spacecraft intended for a flight
toward Mars in the mid-1960s. Pilyugin decided to use a computer
code-named Argon-11, which had been developed under the chief
designer Krutovskikh. A Moscow organization [NIEM, later NICEVT]
was designing computers,
which by their external parameters were quite suitable for use as part
of onboard equipment in spacecraft. And they modified their Argon
computer to adapt it to the kind of problems in which Pilyugin was
interested, and they code-named this new computer Argon-11. These
problems were by and large problems of guidance. This was the first example.
After that, Pilyugin acted in his typical manner, in accordance with
the engineering culture of his firm. He had been designing control systems since 1946,
and he always adhered to idea of building an autonomous control system,
one that would contain within itself all the subsystems necessary to
solve all control problems. This was not an unfounded hope; this was a
definite program. If the development of all subsystems of a control
system is concentrated in the hands of one chief designer, then the
control system can truly be optimized. This makes it possible to
allocate functions among various parts of the system in the most
expedient way in terms of weight, dimensions, energy consumption, and
functional decision-making. Under this approach all
main, as well as auxiliary, parts of the control system are being developed in one organization.
Even before Pilyugin applied this approach to onboard computers, about
five years earlier, he had performed a similar trick with a major, core
component of the control system - the gyroscopic unit. Until the end of
the 1950s Pilyugin's firm had not developed inertial gyroscopic devices.
There were specialized organizations that designed such devices. In
particular, the Chief Designer Kuznetsov's firm developed various
gyroscopic devices for the rocket industry. He also began working on
gyroscopic platforms. In the latter half of the 1950s, Pilyugin
incorporated a gyroscopic platform developed in Leningrad by the Chief
Designer Arefyev into a missile control system. Pilyugin thus acquired
expertise, obtained the results of on-site testing, and later started
the development of gyroscopic platforms in his own firm.
He used the same approach to facilitate the introduction of computers
into the control system. The first experiment that I mentioned - the experiment with
Argon - led to Pilyugin's decision to start the development and
manufacturing of his own computer systems.
For the second phase of the development of the lunar complex N1-L3, Pilyugin
decided to design his own onboard computer. In the first phase, the
control system included some gyroscopic devices of the Chief Designer
Kuznetsov and some analog systems. In the second phase, a totally new control system
was created. This new design was implemented in the fourth (last) launch in
1972. The new control system included a gyroscopic platform and a computing system,
both designed by Pilyugin. This computer, called the S-530, was based on
the Tropa elements. It was intended for calculating all control tasks:
guidance, control of the operating logic of the control system's own
equipment, and control of the engines and of all other systems in the N1
rocket. TThe same computer was to be used in the control systems. Unfortunately, these plans did not
materialize. The fourth launch did not result in the operation of the LOK
or the LK, and therefore no experimental results were obtained about
their control systems from that launch.
Afterwards all control systems developed by Pilyugin included computing systems
designed at his own firm. After the C-530 we developed a computer series
named Bisser: Bisser-2, Bisser-3, Bisser-4, and Bisser-6. The Bisser-6
computer represents today's technological level. Of course, these machines
improved over time. In particular, the scale of circuit
integration increased from medium-scale integration to large-scale
integration to the current solid-state technology of very large scale
integration. This
provided an opportunity to increase the computing resources of the machine,
to enhance its memory, and to raise its speed.
All these systems were based on the same design principle. High reliability was
required of the control system in general, and of the computing system
in particular. Therefore all these systems were designed with
redundancy. They could withstand the failure of any single component. They
had radial interfaces with various exchange devices, such as sensor data converters
and operating component converters.
Along with the introduction of onboard computers, computer equipment was
being installed at ground testing and launch facilities. Here we used the same
approach. During the development of the first rockets, for example,
the N1, the ground facilities used industrial production computers, such as
SM-2 (developed at Severodonetsk). Later on they switched to special
ground models of the existing onboard computers. Those ground models also had
higher reliability. Using the same type of computers made it easier
to establish computer-to-computer communication between the ground and
the board, and this approach is still applied today. Since the structure of
the control system for various space vehicles (with the changes in
rocket stages and cargo weights) has evolved significantly during these
forty years, a whole multi-computer system is now created, which
includes a ground machine and several onboard computers.
Onboard computers could be designed for different purposes, and many
specialized computers were developed. For example, some specialized
computers handled the communications between the central computing
system and various onboard systems, in particular, the radio systems and
the information display and manual control system. Such specialized
computers are of different types, and they may have different time
cycles and interface types. Nevertheless, with the help of appropriate
adapters and coordinating devices, it is possible to create a unified
system. This principle was implemented not only in Pilyugin’s projects.
The Mir space station also included a multi-computer control complex
developed by specialized organizations, in particular, by the Zelenograd
Science Center. It is the same today with the International Space
Station: different types of computers are included in a unified
computing system.
Gerovitch: Researchers from NICEVT,
who developed the Argon-11, say that this computer was installed on
board the Zond spacecraft that circled the Moon.
Priss: Zond is a name for the L-1, which is also our project,
but this happened after the flight toward Mars. Argon-11 was used in
other projects too. Speaking of priority, the very first use of this
computer was on the spacecraft sent to Mars. The L-1 was launched with
the Proton rocket; this project preceded an expedition to the Moon.
There was one successful launch of the L-1, which returned to the Earth
and landed with escape velocity. If this project were to continue, this
computer would have been replaced with the S-530 machine too, but this
did not take place.
Gerovitch: In the initial period, when digital computers were
introduced, what was seen as their advantages in comparison to analog devices?
What were their deficiencies? Was it obvious that a transition to this new
technology was needed?
Priss: At that stage this was not obvious. First, the basic
elements at that time were not sufficiently reliable. There were
numerous failures, and therefore a decision to launch could be made only
when redundant devices were installed. There was hope that back-up
systems would ensure reliable operation in flight. During preliminary
tests all back-up systems, including the computing system, were checked,
and, as a result, a very large number of elements were tested, and
failures occurred more often. For this reason, preparations for the
fourth N1 launch (when an onboard computer was used) proceeded with
great difficulty. Various computer elements failed all the time, repairs
were repeatedly made, and there was always a hanging question whether we
would be able to move on to the next stage in testing.
Second, digital computers at that time did not have any advantageous
external operational characteristics. That is, they were not much
lighter or more energy-efficient than analog systems, and in this sense
there were no advantages. One had to learn how to program them, how to
test algorithms, and how to test software. All this involved great
difficulties, and we placed our hopes on future improvements. At that
time, it was already clear that this technology had good prospects,
since the development of new basic elements was under way. It was clear
that computers would be able to solve many more problems than they did
at the initial stage. Today computers handle control logistics and
systems control, not to mention new, advanced guidance systems, which
would have been very difficult to build with analog devices. Innumerable
changes in the launch inclination, in the direction of flight, in the
trajectory, transitions from one trajectory to another - all this could
in principle be solved with analog methods, but it would have been much
more difficult, not to mention the speed of calculations, which is very
important for logical tasks. It is less important for guidance tasks; in
the latter case, all processes run more slowly, than, say, the processes
of starting-up and regulating the engines. Initially all these problems
were solved with analog methods. As computers improved, these tasks were
shifted on to them, and thus the functions of the control system were
substantially expanded.
TThe use of computers made it possible to eliminate entire classes of
equipment and whole subsystems. For example, today a computer-based
gyroscopic system, incorporated into the control system, fulfills the
task of the initial azimuth aiming of a rocket. All the first rockets of
the 1940s, 50s, and early 60s were aimed with the help of an external
geodetic system, which somehow had to agree with onboard gyroscopic
devices. One had to perform a geodetic locality orientation, one had to
install special geodetic devices on the ground, and then, with the help
of optical communication devices, one could turn and aim the rocket. The
launch installation had to provide means for turning the entire rocket.
Later on the turning operation no longer had to be done on the rocket
itself but was applied just to its gyroscopic system. And when a
computer complex was added to the gyroscopic system, the entire system
was greatly simplified. Onboard pulse generators, which had earlier been
used for timing coordination, were eliminated; electrical current
distributors, which put a cyclogram into effect, were also eliminated -
all this is now done by a computer complex. As a matter of fact, the
computer complex and the gyroscopic system are the only essential
components of the control system; everything else are just various
converters and capacity amplifiers, which control operating components,
rocket automatics, engine automatics, and power source. That’s it.
Actual control problems, which earlier had been solved by complex
devices, are now solved by a computer. Today ground computers prepare
the flight task and recalculate it on the fly if necessary. All serious
functions of the control system are now performed by computers.
Gerovitch: You mentioned that the first computer made at
Pilyugin's firm was built on the Tropa elements, which were not very reliable. When
did the transition to integrated circuits occur? Why did it happen?
Priss: The S-530 computer was developed in the late 1960s, and it
was used on a spacecraft in 1972. Subsequent machines in the 1970s were
based on integrated circuits of various types; the first had
medium-scale integration. Here again Pilyugin chose an original
approach. Different options were available at the time. In our branch of
industry, a new, so-called “open-frame” technology was available: a
designer could build the required circuits with open-frame elements –
tiny diodes and triodes – and thus could in practice, not just on paper,
implement something similar to medium-scale integration elements. This
technology was being used, but not at Pilyugin’s firm. He chose an
alternative method: he let contracts to various specialized
organizations of the Ministry of Electronics Industry. According to his
specifications, large-scale integration elements were developed.
Pilyugin’s firm received finished, well-tested elements, and then
assembled the required units out of those elements. Such was our
approach in the 1970s, and it was used not only at Pilyugin’s firm. In
the late 70s the same approach was used by another firm engaged in the
construction of control systems, the Kharkov Institute [Khartron].
All other design organizations that worked on various elements of a
control system also introduced one technology [of integrated circuits]
or another. The “scattering” technology was widely used with good
results at the Research and Production Association of Measuring
Technology, which built telemetry systems, sensor equipment, transformer
equipment, and so on. I believe they still use this technology. Our
Bisser-6 computer is built on large-scale integration circuits developed
at Minsk or Zelenograd firms.
Gerovitch: The Americans chose integrated circuits as
the basic elements for
the Apollo Guidance Computer in the early
1960s. Was there any study of the American experience? Was it taken into
account? Did it have any impact on technical decision-making?
Priss: I am not aware of that. In 1960s NICEVT was engaged in
this more deeply than we were, and they possibly knew something. In the
past several decades, this information has widely spread. Studies [of
foreign-origin hardware] and comparisons with basic elements and
capacities of our electronic technology are conducted all the time. For
a long time the military system of quality testing blocked applications
of these [foreign] types of systems or elements. Until the last decade,
everything [in the space program] had to pass quality checks by military
organizations, and one of the requirements for control systems was the
use of domestically manufactured basic elements. In recent years this
rule has not been enforced. If such [foreign] technology is used, this
requires detailed knowledge and understanding of what is being done
abroad, and this also requires the creation of domestic analogs to
foreign models. To create an analog takes a lot of time. To repeat
always means to lag behind.
Gerovitch: Was there any discussion of the American design of the control system for
Apollo?
Priss: I do not recall seeing such materials or publications; I
do not think that we had detailed knowledge and understanding of
the hardware implementation of the Apollo control system. There was some information
available about general design solutions and trajectory calculations for Apollo, but
these issues do not belong to the control system.
This information could be of interest only to the lead organization,
which was selecting trajectories and strategies for space flight. Despite
the substantial openness of the Americans and the availability of
endless material on the Shuttle (there was less available on Apollo), there were almost no publications that would specify hardware
design. One could find some general characteristics of the equipment, for example,
the gyroscopic platform or the computer (speed, memory, and so on), but
more substantive information was absent. Perhaps, this information was
available elsewhere, but it did not reach us, the developers.
Gerovitch: Have there been any attempts to compare American onboard
computers with Soviet ones in terms of weight, speed and so on?
Priss: I know that in the early 1980s there were attempts to compare
the parameters of systems designed for Buran and for the Shuttle. And I
must say that, based on external parameters, we did not lag behind. Our machine on
Buran was Bisser-4. In terms of computer performance per se, the
parameters of our machine were close to theirs; perhaps, we even had a
lead. As for the functional operation, here you have to take into
account that the overall structure of our system was different. Speaking
of computers, the overall picture was as follows: there were four machines on
the Shuttle; they worked in the regular mode during the ascent, and they were supplemented with the fifth machine.
This fifth machine was of the same type as the other four, but it had
different software, different "mathematics." It was used as
back-up mathematics in an emergency. According to the American plan, this
back-up mathematics was to be developed by another team, not by those who
did mathematics for first four regular machines. The idea was obvious.
In the American case, a switch to the backup system was to be carried
out by an astronaut. If the astronaut realized that the first system was
not working properly, he could switch manually to the second system. We
did not adopt a similar approach for two reasons. There was no other
organization that could develop the backup mathematics. Even if such an
organization were found, it was still necessary to test and debug their
mathematics. Our testing program included an extensive series of ground
tests and later in-flight tests. The second mathematics would have
required additional spending and cause time delays, and we could not
afford that.
All these issues were widely debated by technical specialists engaged
in the development of Buran. There were many organizations involved. The
lead aviation firm that built the Buran glider and was responsible for
landing strongly insisted on considering this option. But eventually we
managed to prove the reliability of our regular system. Together with
the Rocket-and-Space Corporation Energia, we managed to demonstrate that we
foresaw a large number of potential emergencies, and for all these
potential emergencies we developed automatic modes of coping with them and
rescuing the crew.
For example, we introduced the innovative mode of "restoration of
control" on Buran. Let’s say, for some unclear reason the control system
breaks down in orbit, all four machines break down, the orientation is
lost, the spacecraft begins to make strange and unpredictable maneuvers.
For example, this can happen because of an interruption in power supply.
If power is not restored, even the Americans with their fifth machine
could do nothing. If power is restored, however, then a special mode
would be switched on, which would restore the orientation, tell you
where you are, restore all the processes, and make it possible to rescue
the crew and to return them to Earth.
Nevertheless, the idea of an additional, backup system was discussed
all the time, and as a result, it was implemented - not in hardware, but
mechanically (a hand controller and so forth) on the model 002 intended
for horizontal flight tests. This model of Buran was tested in the
Moscow region with numerous lift-offs and landings. On this model, a
manual landing control mechanism was implemented, but it was never used,
since the automatics worked without failures.
Comparisons were made all the time. Not only the computers were
compared, but also the gyroscopic systems. We had the same amount of
information about their gyroscopic devices. Only external parameters of
the gyroscopic platform were known, not the internal ones. Here we did
not fall behind either. If we take the entire systems - the control
system on Buran vs. the avionics system on the Shuttle - it is
impossible to make an informed, accurate comparison, because there was
no information anywhere on the specific tasks carried out by the Shuttle
avionics system. Based on a rough idea of its composition and on
information from some marginal sources, one could conclude that their
avionics system did not carry out all the tasks assigned to our control
system. Certainly, the avionics carried out guidance and controlled both
automatic and manual modes, but that was all. What else could it do,
what equipment was included in the avionics system to carry out other
tasks - all this was not at all clear.
Except for the gyroscopic platform and the computer,
whose functions were completely clear, all the other equipment [in the
Buran control system] was developed as a complex, that is, it not only
controlled operating components, but also carried out other tasks. A
computer route - stretching from the cabin, where the computing system
was set up, to the exchange devices, which were installed in the tail compartments of
the Buran - transmitted not only information necessary for the control
of aerodynamic surfaces on landing, but also data required for the
control of engines, for the control of small-thrust nozzles, and so on. Therefore,
it would be incorrect to compare our route with the route in the Shuttle
if it did not serve the same function.
Gerovitch: How was the problem of the division of functions between
the human and the machine resolved at different periods? How did the functions of onboard
computers evolve?
Priss: If we talk about the first machines, in the case of the
Mars probe, it was a fully automatic spacecraft. The N1 carrier was also
an automatic system; the orbital ships were supposed to have a pilot and
manual controls, but unfortunately, as I said, they did not get a chance
to be tested. The only case about which I can say anything is Buran. All
the systems designed by our firm before or after Buran are automatic
systems. In
some projects carried out by
the Rocket-and-Space Corporation Energia, on orbital stations, some functions were
assigned to the crew. I do not know the details. I am not aware whether
any such functions related to guidance.
As for the Buran and the lunar ship, they had the so-called "manual
control loop." The implementation of such loops in the presence of an
onboard computer was limited to the following. On Buran, the manual
control system, which included a steering wheel, hand controllers, and
pedals (like on the Shuttle), had two modes of operation: the landing
mode (with tasks similar to aircraft landing) and the orbital control
mode for docking and undocking. There were different types of controls
for these tasks: the aviation controls were the steering wheel and the
pedals, while the orbit controls were the hand controllers in three
dimensions. Inputs from these manual controls through converters were
entered in the computer. There were no special operating components for
manual control; they were the same components that were used in the
automatic mode. It would have been ridiculous to put additional ailerons
or vertical or horizontal rudders [just for manual control].
The main question is this: what algorithms are used to process the information received from manual controls?
There are two possibilities here. The first is this: no function is assigned to the
computer, except for simple transmission, that is, whatever the pilot has
done is transmitted to operating components one-for-one. The second variant
is to limit his possibilities. Say, not to let him give a silly
instruction or an untimely instruction. The latter variant is in fact
chosen. There are some restrictions on the pilot's actions.
Another issue is presenting information to the pilot. During docking, he
must have a visual image of the situation to be able to aim correctly.
Here, too, there are several possibilities. First, he can make
observations through separate optical devices (for example, on Buran,
there was a pilot's sight and some other optics through which he could
observe independently from the computer). Second, he should receive
information about the status of onboard equipment, during the landing
you must show him the landing field, and he must have arrow indicators,
as in an automobile or on an aircraft. The latter task [of information
display] was entrusted to the computer. This information came from
inertial system sensors, from the air-velocity measuring system, and
from telemetry systems, and it fed into the machine. The machine needed
this information for automatic control. But besides this use of
information in the machine, it was also displayed for the pilot.
The Americans assigned a greater role to the pilot than we did, and
the pilot had more opportunities to observe the situation. In the
Shuttle, for example, he even had some indicator panels above his head.
In our case, the setup was a bit different. It was decided from the very
beginning that we would design a shuttle capable of working both in
automatic and manual modes. Therefore, everything had to be automated
for the automatic mode. And so it was done. For example, an automatic
landing system was implemented. Then, when this implementation was
combined with manual control, naturally, an idea arose: since everything
is already in place, the pilot’s role may be limited. Indeed, the
machine thinks faster, it executes commands and evaluates the situation
faster. The Americans faced a different situation, and for this reason
they assigned wider functions to the pilot.
On a lunar complex we had manual control, because landing on the Moon
was to be performed manually. There were special controls made,
information display units, and so on. All this was done through the machine,
in the same way.
Gerovitch: Was the control system for the lunar ship completed?
Priss: It was completed; it passed almost the entire cycle of
testing on the ground. It was ready for operation.
Gerovitch: Let's come back to Buran. If the computer determined
that the pilot was making a potentially dangerous move, what happened in
this case? Would the computer cancel this action?
Priss: No, the computer simply limited the action.
Gerovitch: Say, the pilot could not make a turn by more than a
certain number of degrees?
Priss: He could not make it greater than the number that the machine
accepted.
Gerovitch: That is, the computer physically limited possible changes?
Priss: Yes, it did.
Gerovitch: Was there anything the pilot could do to override it?
Priss: He could not pass the preset limits. He could operate only
within the limits set by the machine, or, more precisely, by the
developer of the algorithm. The pilot could do something else. He could
manually switch to a different control mode. All the modes were
automated and had a specific algorithm (that is, a program). If he had
serious reasons, he could, for example, cancel docking. Say, he is on a
shuttle which is docking with a station in the active mode, and he
receives information - either from the station, or from the ground -
that for some reason the docking cannot be performed, while the docking
has already began. He can manually cancel this mode and switch to
another. He can choose the control mode. This switch could be performed
either automatically according to machine criteria, or by a command from
the ground, or by the cosmonaut.
Gerovitch: That is, the cosmonaut could only switch between the
modes, but could not turn off the computer altogether?
Priss: In principle he could turn it off, but this did not make
any sense.
Gerovitch: Who was doing programming for the onboard machine on
Buran?
Priss: This is a very broad issue. If we talk about small
projects, such as the Mars or the N-1 (in terms of computing and
programming tasks, those automatic projects from today's perspective
were not so big), then the development of mathematics was done as
follows. There are three circles of programs for the machine.
The first circle is a set of tools for the machine itself. The machine
must have an operating system, which directs the computing process: how
to address various types of memory and how to receive and send out
external data; there are also channel programs, input-output programs,
and so on. All this mathematics does not depend on the task carried out
by the machine. It must control the execution of any task assigned to
the machine. A special group of programmers is assigned to create this
set of tools. They are “pure” programmers who must know the computer,
its system of instructions, and the interfaces very well. One must add
to this set also the algorithms of flight mission input, flight mission
control, and exchange with other machines (if this is multi-machine
system, then some computers must be active, and some passive, and so
on). This set of [general] programs is required for every type of
computer. If I shift this machine from one set of [specific] tasks to
another, this set of [general] programs will remain the same.
The second circle comprises guidance tasks. This includes the
processing of information from various sources (inertial systems, optical systems,
and telemetry systems). Then the computer solves the guidance problem,
taking into account various dynamic characteristics of the object of
control: inertial and weight characteristics of the spacecraft, the characteristics of
various operating components, dynamics requirements, and limitations
imposed by the rocket design (for example, there are limitations on
rotation angles and rotation speeds). The programs that we include under the
guidance rubric, as a rule, are developed by programmers from the main
contractor organization that designs the control system. If we design the control system,
then these are our programmers.
Gerovitch: Are these programmers trained as engineers? Do they understand
the logic of the control system well?
Priss: Certainly. They design it! They design guidance
algorithms. For example, one can direct a flight along a fixed trajectory,
in which case any deviation from this trajectory is detected by sensors, and then the
spacecraft must return to the straight path that you have planned beforehand.
This is yesterday's technology; nobody does this today. Today science
has developed the technique of terminal
control: it does not matter how I fly; what is important is that I
arrive in the final destination with the given speed, angular
parameters, and so on. This means that I don't have to force the product, to twist it
this way and that; I save fuel and power; I don't have to make an extra
durable spacecraft that would resist the wind. If the wind carries you
away, you don't have to fight it; you can correct for it later. This is the meaning
of terminal
control.
Programming is done by people who know, understand, and can do all of
this. Besides, they know the computer and its operating system; they know
the capacities of the machine. They try to solve problems without
spending much memory or processor time, that is, they try to make an
optimal use of its resources. As initial data, they use specific
trajectory requirements set by the developers.
There are some exceptions to this approach. For example, V.A.
Trapeznikov's institute, that is, the Institute of Automation and Remote
Control [currently the Institute of Control Problems], develops
mathematical models of complex dynamic processes for large rocket
complexes. In particular, they develop algorithms for regulating the
propellant component ratio for rocket engines. This line of research was
started there by the academician B.N. Petrov. They do the initial
development of such algorithms and then transfer further development to
our specialists, who link these algorithms with their own algorithms
that relate to motion. For example, if an engine is regulated, then
velocities also change, and these algorithms must be coordinated.
The third group of programmers deals with the issues of control of
all other flight-related processes, with the control of other onboard
systems. Such issues also have two parts. Say, a developer of the
control system formulates an algorithm of engine control and
requirements for the separation [of stages]. For example, there are
certain strength requirements for the separation. Here the third group
of programmers must come into contact with the second group. For
example, the task is to turn off the engine when a certain velocity is
reached. Velocity is measured by dynamics specialists, but they don't
know how to turn off the engine. This task is not a simple instruction
but a whole cyclogram. The dynamics specialists only issue a command to
turn off the engine, while the entire cyclogram - all the subsequent
operations with the engine, with separation, and so on - is done by
integration programmers, who know little about motion and dynamics but
understand the logic of operation of the system as a whole.
It was precisely at this stage that the developers of Buran faced
tremendous problems caused by the very scale of the task. There were 52
onboard systems that had to be controlled by the computer complex. Some
of them were part of the control system, and some were not. Take, for
example, the telemetry system. It has its own chief designer who creates
the hardware and knows how it should function. Telemetry must be turned
on and off, it may work in different regimes, and so on. Only its chief
designer knows the algorithm of working with this system, but it is the
computer that will actually be operating it. This means that there must
be a separate program for the telemetry system. To find a place for this
program and to agree upon its interaction with other programs is a task
of the integration programmers working for us. Then a question arises:
who will write this specific program? On simpler spacecraft, where we
faced relatively few such problems, we used the following method. The
developer of a system draws a conventional cyclogram, without
translating it into a software program, and then our integration
programmers translate it into a program. This method always resulted in
discrepancies, misunderstanding, and errors, and several iterations were
needed to correct and debug it.
It was not feasible to use the same method on Buran: in this case, the
design stage would have taken 20 years. For this reason, high-level
programming languages were created that enabled the developer of a
system to write up an algorithm without knowing any characteristics of
the computer, its system of instructions, or any other internal
requirements of the machine. He would write an algorithm in a simple,
clear language, and then a programmer on the basis of this initial
material would write a program for the machine. During the design of the
Buran, the translation of this algorithm into a program was done mainly
by hand with the help of some semi-automatic tools. Today new systems
exist that can process this information and produce a complete program
as a result. After that, this program, of course, has to be tested:
first on specialized simulators, and then on integrated simulators. In
my recent article, I have included a list of organizations involved in
this project as part of the Buran program [G.M. Priss, "Nekotorye aspekty razrabotki sistemy
upravleniia 'Burana'," Aviakosmicheskaia tekhnika i tekhnologiia,
no. 3 (1999): 35-42.].
Gerovitch: Did the Institute of Applied Mathematics take part in
this project?
Priss: Yes, they participated most actively. The academician A.N.
Tikhonov supervised this project; M.R. Shura-Bura was among his top
aides. They worked together with us, since our specialists knew the
specific characteristics of the computers. They created the PROL language
for programming this type of tasks - not guidance problems, but logical
problems.
Gerovitch: Could you tell more about the Bisser computers?
Priss: Bisser-1 did not develop beyond the design phase. Bisser-2
was designed in the late 1970s-early 80s, and until recently it was
installed on Zenit-2 rockets. This machine was used quite widely and was
installed on many different models. The development of Bisser-3 went in
parallel with the work on Bisser-4 for Buran. These two machines were
principally different. Bisser-3 was also widely used. Today it is
installed on Zenit-3, on the boost stage of the Sea Launch. It also flew
on the Fregat boost stage; there have been four joint launches with the
French.
Bisser-4 stood apart from these models; it was an original machine.
It was used only on Buran. Its main feature was that each channel was
structurally autonomous, that is, each channel was a separate machine.
It was possible to combine as many of them as necessary. There were four
machines in one complex and four machines in the other complex, and a
special external logical switchboard implemented the majority vote
output.
Gerovitch: Would it have been possible to install five machines?
Priss: Yes, it would have. The only thing that would have change
is the logical switchboard so that it could process information from
five sources. It would have also been possible to install only three
machines. Our choice of this logic was influenced by the American
structure. They have a fifth machine, and it works according to its own
program. But since it uses a different program, it is impossible to
apply the majority vote rule. This principle requires a comparison of
similar information from all sources and suggests choosing the outputs
that are identical. For example, out of three machines two results must
be identical; if one output is different, then I simply stop paying any
attention to it and take information from the other two. Out of four
machines, three results must be identical. It is possible to build more
complex logic: to compare pair by pair and so forth. But if the fifth
machine has its own program, it cannot be part of this process. Before
producing the final output, all the computers in the Bisser-4 complex
exchange information among themselves. This way the reliability of this
system sharply increases.
In all current models Bisser-3 is used. The next step is Bisser-6
machine on integrated circuits of higher integration scale, newly
developed by organizations in Minsk and Zelenograd. This computer has
improved communication with external users, a higher speed, and a
different type of memory. So far this machine has been used in ground
testing complexes. It is hardware- and software-compatible with Bisser-3
(with small adjustments). When the testing is completed, it can be
installed on all models where currently Bisser-3 is used. Bisser-6 is
cheaper, its elements are smaller, and it is lighter and more
power-efficient. It is our next step.
Gerovitch: Does the Bisser-6 complex operate on the same principle
as Bisser-3, that is, its computers are integrated, rather than
autonomous?
Priss: Yes, that's right.
Gerovitch: Let's go back to Bisser-4. Say, one of four machines
produces an output that differs from the others. Would this machine be
turned off completely, or only its output during this one cycle would be
discarded?
Priss: Only the output during this cycle would be discarded. This
could be a sporadic malfunction, and the computer may operate normally
in the future.
Gerovitch: Would this machine be included in further operation on
a par with the others?
Priss: Yes, of course.
Gerovitch: Were there any computer malfunctions during the Buran
flight?
Priss: On Buran there was not a single malfunction - not only in the computer, but in
the entire control system. The entire prelaunch testing cycle was repeated twice. The
first launch of the Energiya booster with Buran was scheduled for
November 30, 1988. But they called it off right on the pad. The system
did not take off because the mechanism for retracting the targeting
optical devices on the booster malfunctioned; I already talked about it
earlier.
Today optical systems are not used during launches. Our gyroscopic
platforms have a gyro-compass mode, that is, the platform itself can
determine the cardinal points; there is no need for geodesic or optical
devices. Wherever the platform is, it will determine its location and
direction of movement. The Americans did not have that, and they had to
do aiming. The matter is that the Americans do not have a booster rocket
separate from the Shuttle. They have solid-fuel boost engines and a tank
that works with the Shuttle engine. Therefore, a control system - the
“brain” - is installed only on the Shuttle. They had three gyroscopic
platforms, and it was necessary to aim them. For this purpose they used
a ground optical system. But they were able to put their platform on the
left side of the cabin and somehow managed to establish an optical link
with the ground to aim correctly.
We have not been able to place our gyroscopic devices on the Buran in a
similar way. This happened not because our platform is bigger; in fact,
it is rather smaller than the American one. The matter is that the requirements
for automatic operations - including such operations on the orbit as
docking, determining the location, and so on - resulted in expanding the structure of
the control system with a whole complex of automatic optical devices:
stellar-solar gauges, navigation antennas, and so forth. It was
necessary to be able to adjust their position with relation to the platform. All
our gyroscopic devices were installed not in the front, but behind the cabin, in
the cargo compartment. Three platforms (a triple-redundancy system) and all optical
devices were put on a very powerful adjusting plate. But the cargo compartment is closed!
It opens only on the orbit. And they were not able to make a slit to reach these devices.
At that time, we did not have platforms with the gyro-compass mode. We
needed an optical orientation to set the initial azimuth, but this could
not be done. Therefore, we had to do optical orientation for the platform
that stood on the rocket.
Our Energiya rocket had its own control system, separate from the
shuttle (which the Americans did not have), and therefore Energiya could
be launched without Buran. Its gyroscopic system had to be aligned. A
ground optical station aligned it with the help of special optical
devices. We had to aim two beams at each platform, and there were three
platforms in total. On the N1 we solved the same problem. An optical
alignment device was created, which was needed only on the ground. It
was not needed in flight, because the rocket had already been aligned
and took off. On the N1 we simply dropped this device; it fell on the
ground and shattered into pieces. It could be used only once. This was a
waste, and we decided to preserve such devices on Energiya. On the N1
this would have been impossible: the devices were placed too high, the
service trusses moved away, and there was nothing that could pick up
those devices. With Energiya, an opportunity presented itself. Energia
was much shorter, smaller than the N1. A special truss construction was
designed that supported those three devices. It was fastened to the
rocket, but at launch it would automatically separate by way of
pyrotechnical locks and move away from the rocket.
During the first attempted launch on October 29, 1988, this system did
not work. More precisely, the disconnection occurred, but there was a
tilt, and a confirmation that it worked did not come through. The launch
was aborted. But up to that moment all preparations on board passed without
a flaw. Then the fuel tanks were emptied, and another attempt was
scheduled in two weeks, for November 15. We repeated the entire routine.
This time this gizmo worked and moved away, we reached the orbit, flew
two orbits, and then began slowing down and descending. At this stage,
there were other difficulties. We landed in the automatic mode. There
was a side wind of 17 meters per second, but we landed within three
meters of the mid-line of the landing strip. Not a single flaw! There
was none - either at the take-off, or during the ascent, or during the
flight.
Gerovitch: What was Sergei
Korolev's opinion on the prospects of using onboard computers? He
evidently had contacts with the design bureau of Philip Staros and
Joseph Berg in Leningrad and asked them to develop an onboard computer
in the mid-1960s. Some people contend, however, that he was skeptical
about onboard computers. Do you know what
his opinion was? To what extent could his opinion have influenced Pilyugin's
decisions?
Priss: Pilyugin always was on very terms with [Sergei
Pavlovich] Korolev. They were friends,
and therefore Pilyugin always listened to Sergei Pavlovich's opinion.
They never disagreed on principal issues. They had some disagreements on
specific questions. They often had quite harsh and vigorous disputes. But
Korolev died in 1966. It was just the beginning. I was pretty close to
the these circles, and I never heard of Sergei Pavlovich's negative
attitude toward computing.
I am not aware of the contacts that you mentioned. I can only make
the following assumption. At that time Sergey Pavlovich's organization
had already formed a large division under the direction of Boris
Yevseyevich Chertok. They too were designing control systems. This
happened for the following reason. When Korolev started the development
of manned spacecraft, he offered Nikolay Alekseyevich [Pilyugin] to
build control systems for them. From the point of view of control,
satellites are very different from manned spacecraft; satellites are
rather passive objects. Before that, nobody else designed control
systems. In the late 1950s, however, a firm in Kharkov was created to
build control systems for the Chief Designer Mikhail Yangel. In the same
period, a special design bureau under the direction of Nikolay
Semikhatov was set up in Sverdlovsk; they began doing the same for the
Navy. And the directors of both firms were former employees of our
organization.
The period when Sergey Pavlovich offered Nikolay Alekseyevich to
participate in this project was very difficult for us in terms of work
load and also personal relations. Gagarin flew in 1961. His spacecraft
was a primitive device. He landed on a parachute; the spacecraft had
almost nothing to do. Korolev envisioned a whole series of advanced
piloted spacecraft, and later this was indeed implemented. At that very
moment [the Chief Designer] Vladimir Chelomey began working on
spacecraft, and Pilyugin was assigned to do some projects for him. Thus
we did work for Korolev, Yangel, and now Chelomey. Pilyugin realized
that he could not carry out all these projects at the same time, and he
declined Korolev's offer.
Sergey Pavlovich began working on this problem in his own
organization. Boris Chertok, Boris Raushenbakh, and others were
involved. Apparently, they coped well, and this division still exists
and solves these problems with good results, which are in no way
inferior to what we could do. There is, however, a difference in
approach. We work by the method I described earlier: we gather
everything under one roof. What they do is, in effect, a compilation.
They buy a machine; they buy gyroscopic devices; they buy optical
equipment, and so on. We try to build everything ourselves, except for
the optical devices. Apparently they realized, just as we did, that it
was necessity to use computer technology. I never heard anyone,
including Sergey Pavlovich, to speak against it. He was not in this
sense conservative, and I can hardly believe that he could have taken a
negative stance. Both he and Chertok understood all these problems
perfectly well. It is hard to imagine now that someone could have
objected [to the use of computer technology].
Gerovitch: By the mid-1960s, analog technology had achieved a
certain level of reliability, while the new digital technology might
have raised doubts. It is often said that Korolev insisted that it was
necessary to rely on well-tested technologies, to choose simple
solutions without unnecessary complications.
Priss: This principle has always held true. Everyone supports it.
In this sense the West is more conservative than Russian engineers. We
now often face this problem. Today negotiations are going on with
Boeing, which has created the Sea Launch company, about further steps,
in particular, to work not just on a sea launch, but also on a ground
launch. We put forward various proposals, for example, switching to
Bisser-6. They replied, "No
need for that! The old computer has already flown, and the new one has
not." We said, "It will be well tested by the deadline!" They reply:
"No; there is no need for that." I believe they have the rule that all new
models must have no less than 70% of old equipment. But even in the
remaining 30% one might include a computer.
Gerovitch: Thank you very much for the interview.
|