Research Focus
In my work, I aim to create experimentally-validated analytical models to enable the design and advanced manufacturing of high-performance materials, which have broad applications in the electronics, healthcare & life sciences, automotive, aviation & aerospace, and energy sectors. My research, which has a strong emphasis on process development and property prediction/tuning, investigates materials synthesis, recyclability & sustainability, and process-structure-property characterization, with a central focus on powders, plastics, adhesives, and films, as well as nanotubes/nanofibers, graphene, aerospace-grade polymers, and ceramics. These can be combined to form a variety of material systems with enhanced performance and manufacturability. In pursuit of creating materials by-design, my work employs nanomaterial & polymer processing and post-processing techniques, plasma technology, patterning and self-assembly, composite fabrication and testing, and multi-scale characterization to quantify structural, thermal, rheological, mechanical, and electrical properties. These are used to design a variety of high-strength, lightweight, and high-temperature materials, including powders, metals, adhesives & multilayer polymer films, ultradense nanofiber thin films, carbon nanotube (CNT)-reinforced polymer and ceramic matrix nanocomposites, recyclable materials, and a range of nanomaterials for innovative and sustainable commercial applications.
Selectively tuning the substrate adhesion strength of aligned carbon nanotube arrays via thermal post-growth processing
The excellent intrinsic properties of aligned nanofibers, such as carbon nanotubes (CNTs), and their ability to be easily formed into multifunctional 3D architectures motivates their use for a variety of commercial applications, such as batteries, chemical sensors for environmental monitoring, and energy harvesting devices. While controlling nanofiber adhesion to the growth substrate is essential for bulk-scale manufacturing and device performance, experimental approaches and models to date have not addressed tuning the CNT array-substrate adhesion strength with thermal processing conditions. In this work, facile 'one-pot' thermal post-growth processing (at temperatures Tp = 700-950°C is used to study CNT-substrate pull-off strength for mm-tall aligned CNT arrays. CNT array pull-off from the flat growth substrate (Fe/Al2O3/SiO2/Si wafers) via tensile testing shows that the array fails progressively, similar to the response of brittle microfiber bundles in tension. The pull-off strength evolves non-monotonically with Tp in three regimes, first increasing by 10x through Tp = 800°C due to graphitization of disordered carbon at the CNT-catalyst interface, then decreasing back to a weak interface through Tp = 950°C due to diffusion of the Fe catalyst into the substrate, Al2O3 crystallization, and substrate cracking. Failure is observed to occur at the CNT-catalyst interface below 750°C, and the CNTs themselves break during pull-off after higher Tp processing, leaving residual CNTs on the substrate. Morphological and chemical analyses indicate that the Fe catalyst remains on the substrate after pull-off in all regimes. This work provides new insights into the interfacial interactions responsible for nanofiber-substrate adhesion and allows tuning to increase or decrease array strength for applications such as advanced sensors, energy devices, and nano-electro-mechanical systems (NEMS).
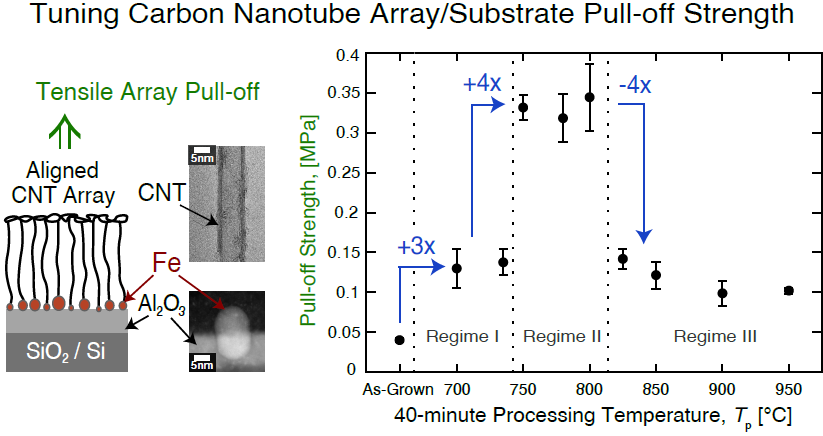
Extreme hardness in ultra-low density carbon matrix nanocomposites reinforced by high packing fraction aligned carbon nanotubes
Polymer-derived pyrolytic carbons (PyCs) are often desirable for low density high-temperature structural applications when they can be reinforced with high stiffness and strength fibers to address brittleness. Nanofibers, such as aligned carbon nanotubes (A-CNTs), can be an ideal reinforcement owing to their high mass-specific properties, and while modeling suggests that properties of A-CNTs at high volume fractions (i.e., 10-30 vol%) could yield significant enhancements, it is unknown how CNT confinement influences processing, as such materials have never been synthesized. Here, we report process development demonstrating the first successful fabrication of fully infused, void-free A-CNT carbon matrix nanocomposites (A/C-NCs) via polymer infiltration pyrolysis (PIP) that establishes a platform to study nanofiber-reinforced polymer-derived ceramics. The size of the average A/C-NC graphitic crystallites increases as CNT vol% increases up to 30 vol%, and the inter-layer separation of the PyC graphitic crystallites decreases, evidencing a nanoscale confinement effect observed in concert with increased mechanical performance. Vickers microhardness testing in the axial CNT direction of A/C-NCs shows agreement with prior data for low vol% CNTs in PyC and mechanical modeling, where specific hardness increases from 3.3 GPa/(g/cm3) for PyC to 6.7 GPa/(g/cm3) for 30 vol% A/C-NCs, demonstrating A/C-NCs as an advantaged superhard lightweight material.
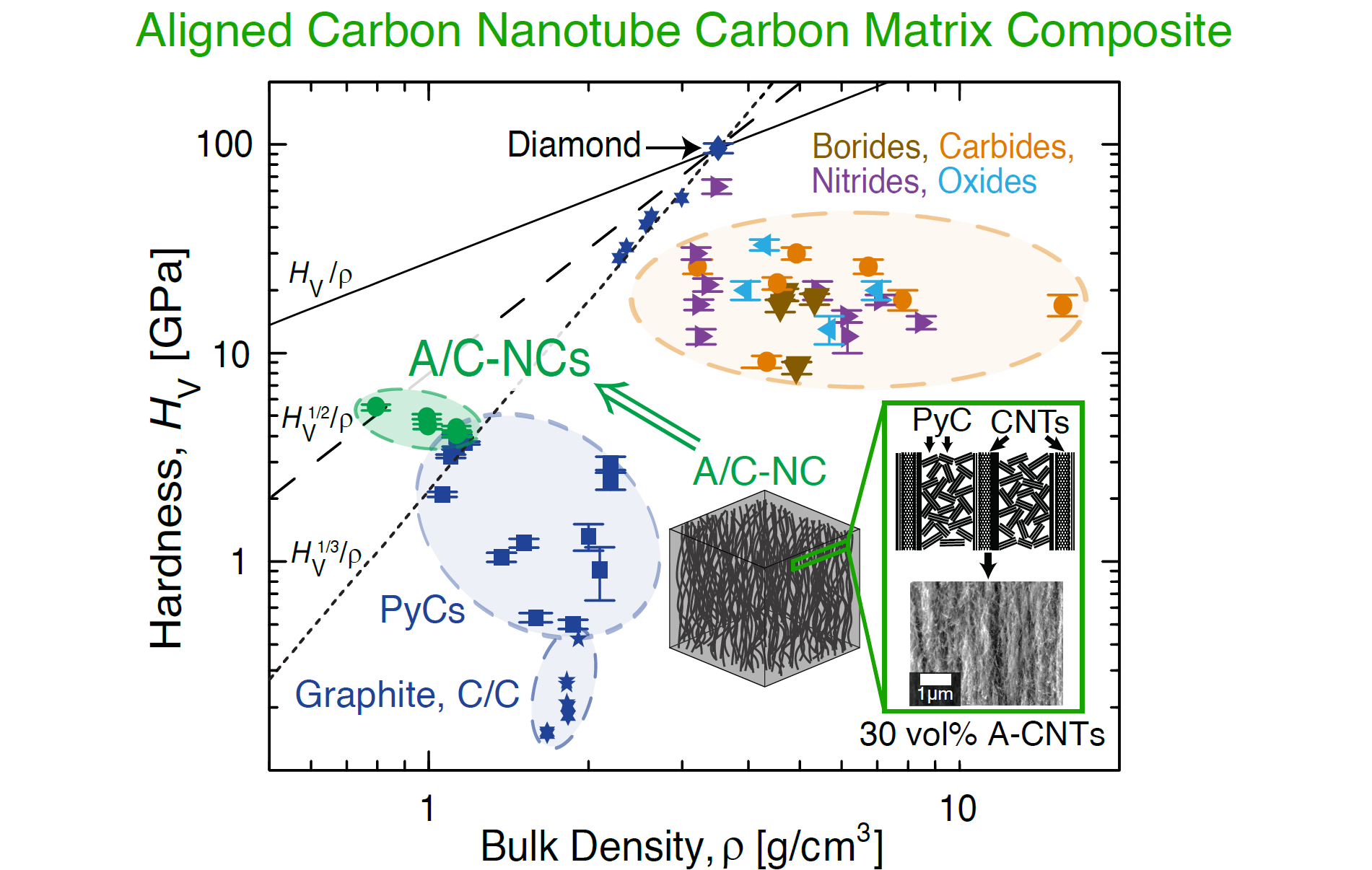
High-volume-fraction textured carbon nanotube–bis(maleimide) and −epoxy matrix polymer nanocomposites: Implications for high-performance structural composites
Polymer matrix nanocomposites (PNCs) incorporating high volume fractions (Vf in excess of 10 vol%) of aligned carbon nanotubes (A-CNTs) are promising for high-performance structural composite applications leveraging texture for multifunctionality and performance-to-weight ratios. However, to enable manufacturing of scalable structures using A-CNT PNCs, nanoscale confinement and interfacial effects due to high A-CNT content in aerospace-grade polymer matrices need to be better understood. Here, we report model-informed fabrication of high CNT Vf PNCs to develop process-structure-property relationships, including a scaled film and laminate technique for A-CNT polymer laminates, and the fabrication of microvoid-free and fully infused bismaleimide (BMI) and epoxy PNCs with high packing densities (volume fractions) of biaxially mechanically densified mm-tall A-CNT array reinforcement (1 to 30 vol%, corresponding to average inter-CNT spacings of ~70 to 6 nm). A polymer infusion model developed from Darcy's law accurately predicts the time for resin to infuse into CNT arrays during capillary-assisted PNC processing, corroborated by experimental observations via X-ray micro-computed tomography and scanning electron microscopy that a diluted resin with ~10x lower viscosity than neat resin is required to obtain complete infusion into high CNT Vf A-CNT arrays (10-30 vol%). For each tested A-CNT vol%, the cured PNCs maintain vertical CNT alignment and glass transition temperature, and the decomposition onset temperature remains constant for epoxy PNCs but increases by ~8°C for 30 vol% A-CNT BMI PNCs compared to the neat resin. For both polymer matrix systems, a ~2x increase in the axial indentation modulus for 30 vol% A-CNT PNCs compared to neat resin is measured, and no significant change in transverse A-CNT modulus is shown experimentally and via modeling, indicating that reinforcement with A-CNTs at higher Vf leads to enhanced anisotropic mechanical properties. Through the process-structure-property scaling relations established here, this work is envisioned to support the development of next-generation structures comprised of nanomaterials with enhanced performance and manufacturability.
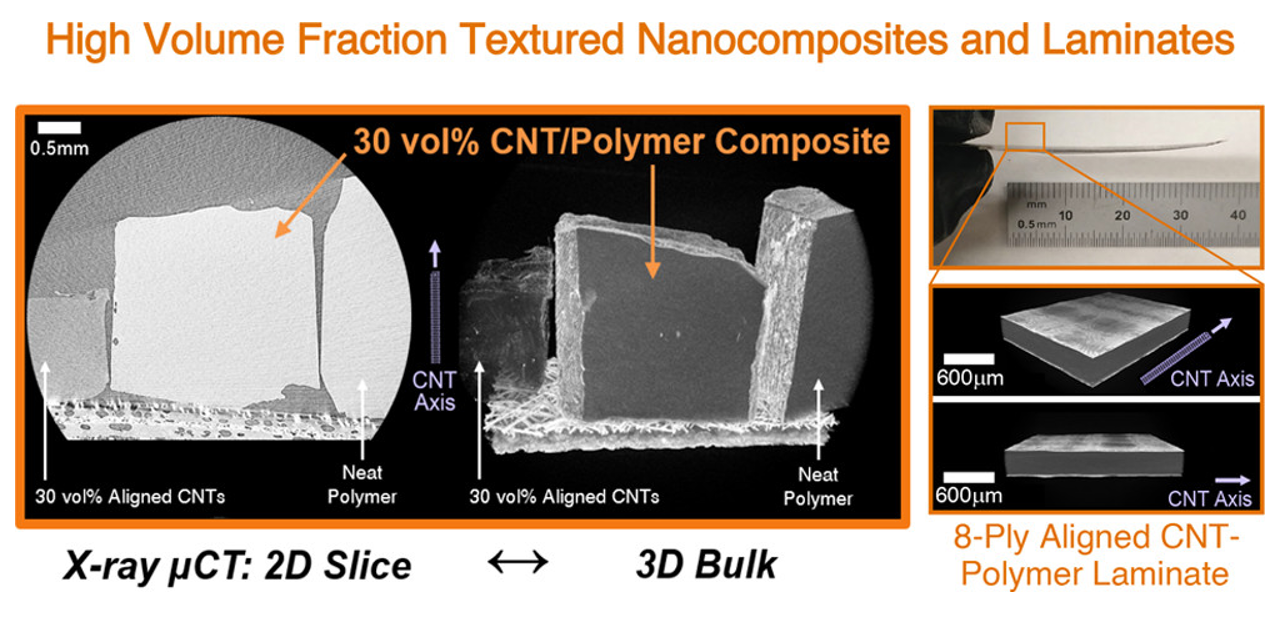
Substrate adhesion evolves non-monotonically with processing time in millimeter-scale aligned carbon nanotube arrays
The advantaged intrinsic and scale-dependent properties of aligned nanofibers (NFs) and their assembly into 3D architectures motivates their use as dry adhesives and shape-engineerable materials. While controlling NF-substrate adhesion is critical for scaled manufacturing and application-specific performance, current understanding of how this property evolves with processing conditions is limited. In this report, we introduce substrate adhesion predictive capabilities by using an exemplary array of NFs, aligned carbon nanotubes (CNTs), studied as a function of their processing. Substrate adhesion is found to scale non-monotonically with process time in a hydrocarbon environment and is investigated via the tensile pull-off of mm-scale CNT arrays from their growth substrate. CNT synthesis follows two regimes: Mode I ('Growth') and Mode II ('Post-Growth'), separated by growth termination. Within 10 minutes of post-growth, experiments and modeling indicate an order-of-magnitude increase in CNT array-substrate adhesion strength (~40 to 285 kPa) and effective elastic array modulus (~6 to 47 MPa), and a two-orders-of-magnitude increase in single CNT-substrate adhesion force (~0.190 to 12.3 nN) and work of adhesion (~0.07 to 1.5 J/m2), where the iron catalyst is found to remain on the substrate. Growth number decay in Mode I and carbon accumulation in Mode II contribute to the mechanical response, which may imply a change in deformation mechanism. Predictive capabilities of the model are assessed for previously studied NF arrays, suggesting that the current framework can enable the future design and manufacture of high-value NF array applications.
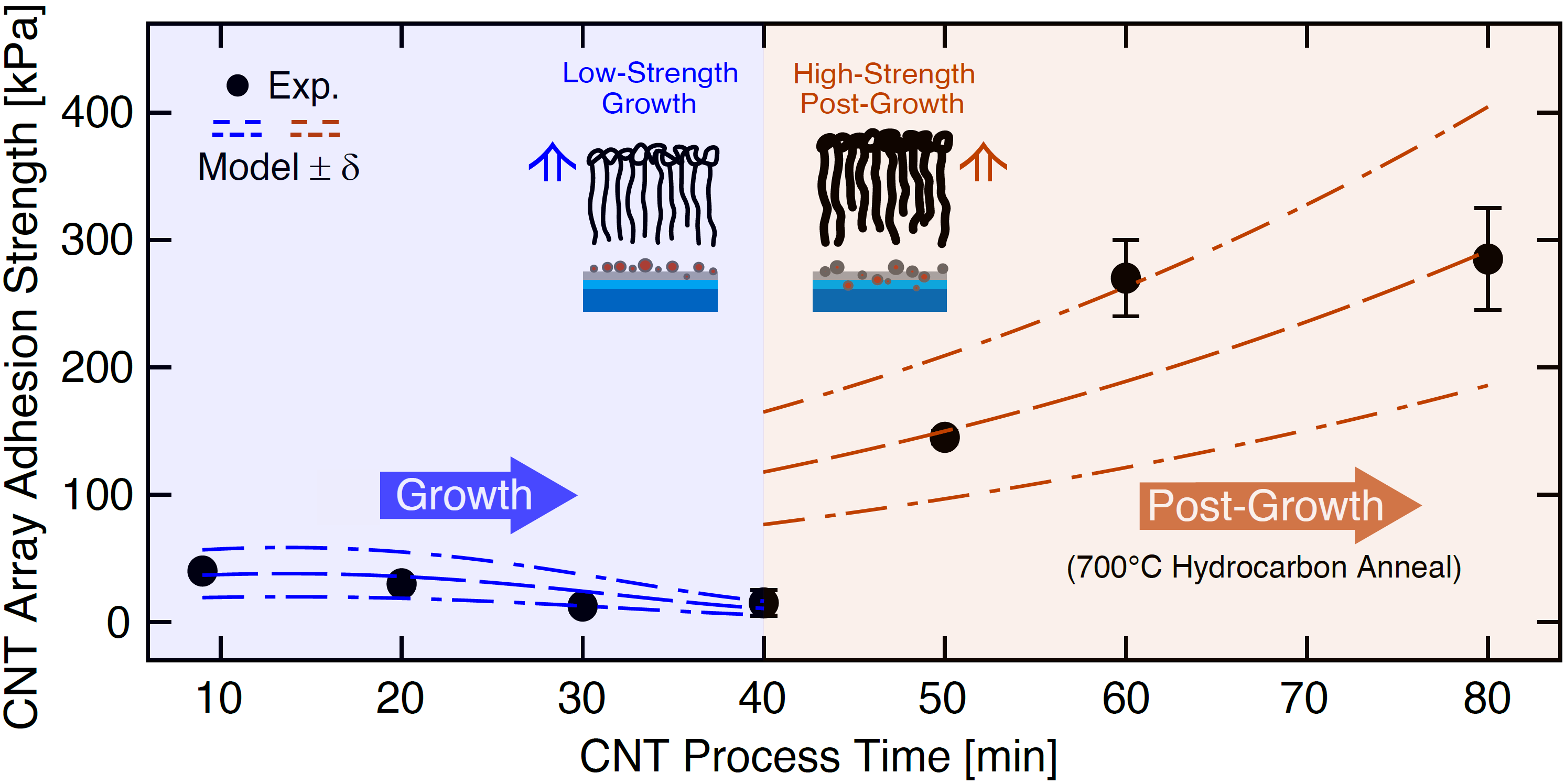
Morphology control of aligned carbon nanotube pins formed via patterned capillary densification
While a variety of self-assembled carbon nanotube (CNT) structures, such as cell networks, micropillars, and pins have previously been fabricated via the capillary-mediated densification of patterned CNT arrays, predicting the critical pattern size (scr) that separates cell versus pin formation and the corresponding process-morphology scaling relations within the micrometer range are outstanding. Here, facile and scalable mechanical patterning and capillary densification techniques are used to establish scr by elucidating how the effective elastic modulus of aligned CNT arrays during densification governs the resulting pin geometries. Experiments and modeling show that this effective modulus scales with CNT height and is about an order of magnitude smaller for pins as compared to cell networks formed from bulk-scale (i.e. non-patterned) CNT arrays. Patterning therefore results in pins with a lower packing density (commensurate with double the wall thickness) and a larger characteristic length scale than bulk cell networks (i.e. scr ~ 5x cell width). CNT arrays with the randomly-oriented carbon crust removed via oxygen plasma etching yield a higher degree of structural uniformity and better agreement with the proposed elasto-capillary model, which enables the use of capillary densification to predictively design hierarchical and shape-tunable materials for advanced thermal, electronic, and biomedical devices.
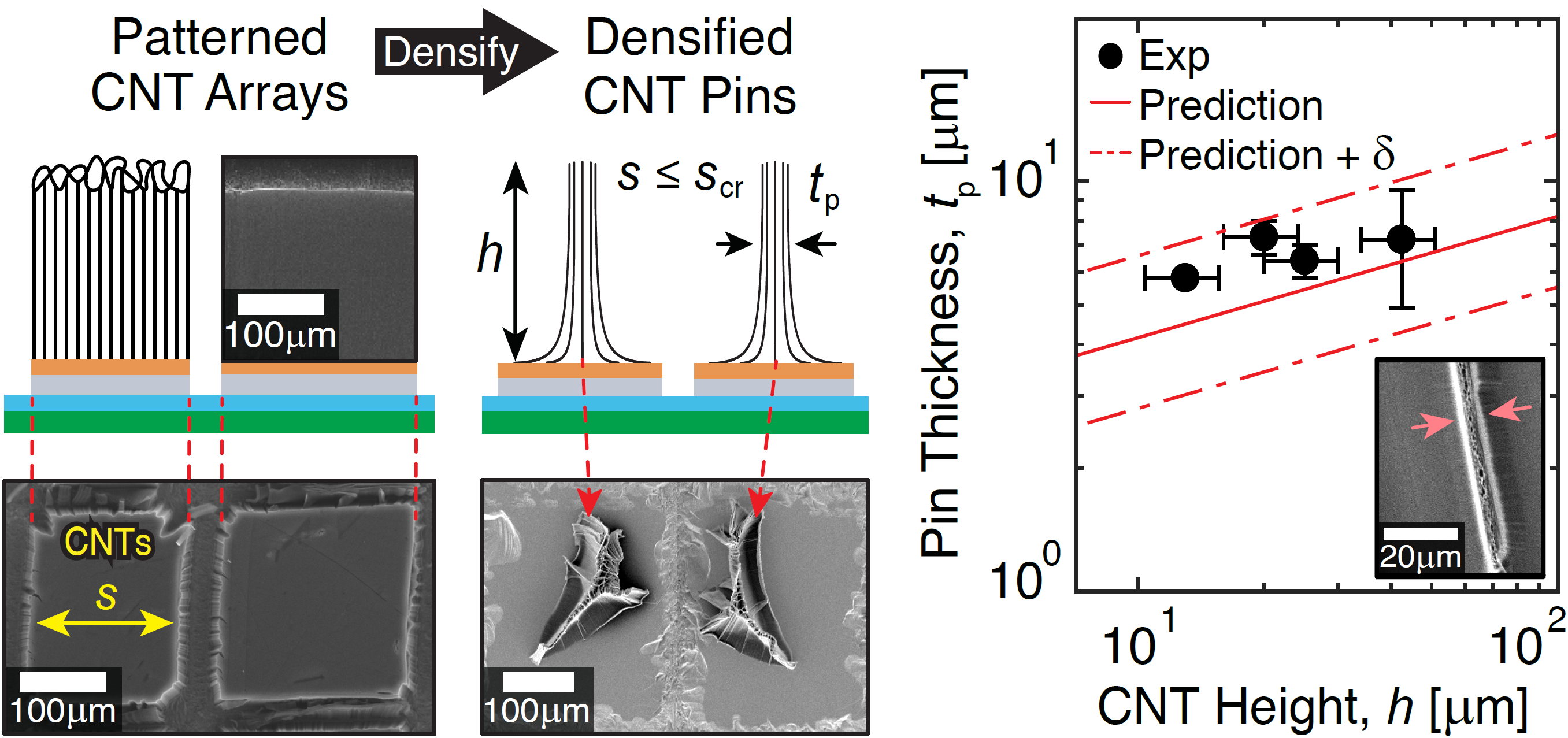
Process-morphology scaling relations quantify self-organization in capillary densified nanofiber arrays
Capillary-mediated densification is an inexpensive and versatile approach to tune the application-specific properties and packing morphology of bulk nanofiber (NF) arrays, such as aligned carbon nanotubes. While NF length governs elasto-capillary self-assembly, the geometry of cellular patterns formed by capillary densified NFs cannot be precisely predicted by existing theories. This originates from the recently quantified orders of magnitude lower than expected NF array effective axial elastic modulus (E), and here we show via parametric experimentation and modeling that E determines the width, area, and wall thickness of the resulting cellular pattern. Both experiments and models show that further tuning of the cellular pattern is possible by altering the NF-substrate adhesion strength for aligned NFs (here carbon nanotubes) grown via chemical vapor deposition, which could enable the broad use of this facile approach to predictably pattern NF arrays for high value applications.
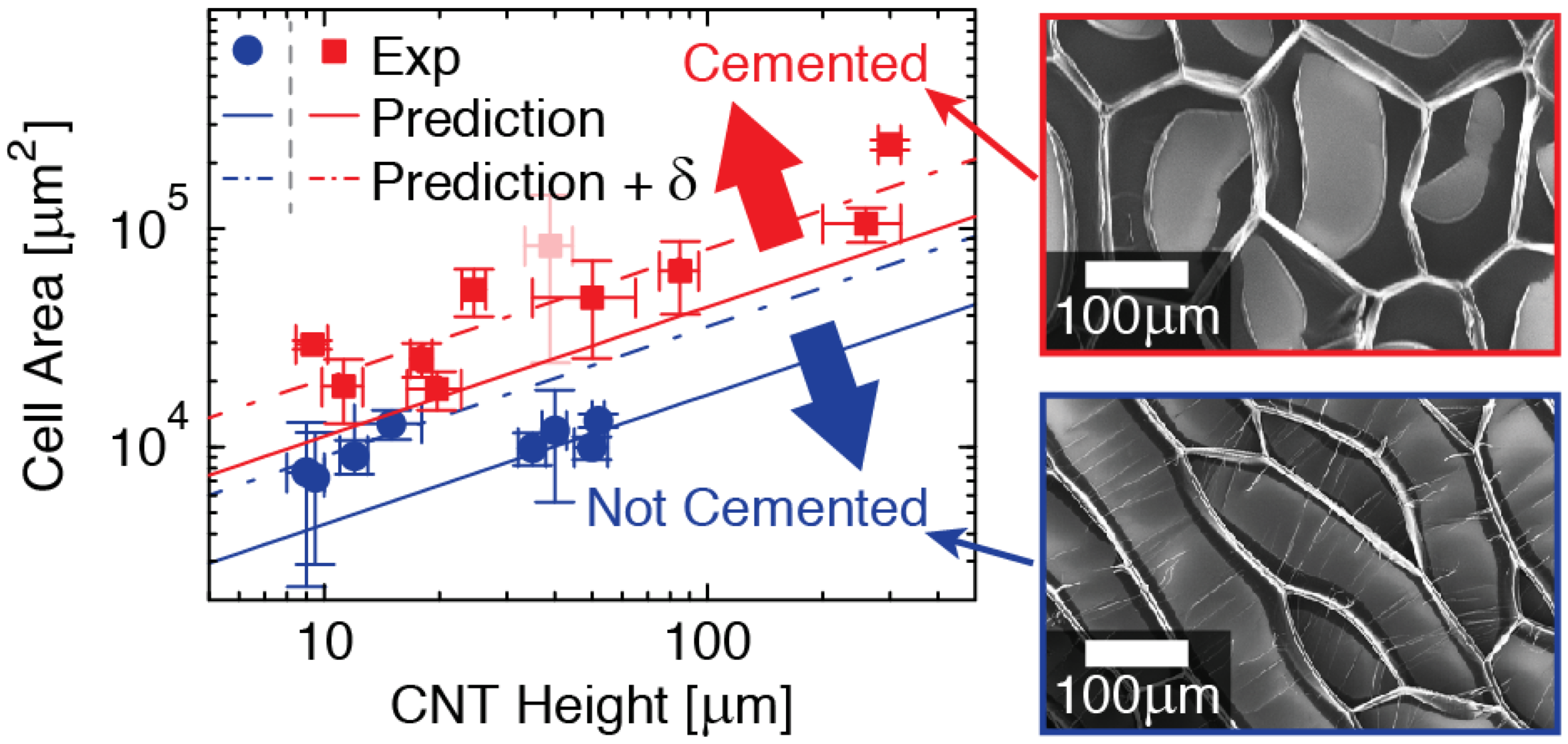
Mesoscale evolution of non-graphitizing pyrolytic carbon in aligned carbon nanotube carbon matrix nanocomposites
Polymer-derived pyrolytic carbons (PyCs) are highly desirable building blocks for high-strength low-density ceramic meta-materials, and reinforcement with nanofibers is of interest to address brittleness and tailor multi-functional properties. The properties of carbon nanotubes (CNTs) make them leading candidates for nanocomposite reinforcement, but how CNT confinement influences the structural evolution of the PyC matrix is unknown. Here, the influence of aligned CNT proximity interactions on nano- and mesoscale structural evolution of phenol-formaldehyde-derived PyCs is established as a function of pyrolysis temperature (Tp) using X-ray diffraction, Raman spectroscopy, and Fourier transform infrared spectroscopy. Aligned CNT PyC matrix nanocomposites are found to evolve faster at the mesoscale by plateauing in crystallite size at Tp ~800 °C, which is more than 200 °C below that of unconfined PyCs. Since the aligned CNTs used here exhibit ~80 nm average separations and ~8 nm diameters, confinement effects are surprisingly not found to influence PyC structure on the atomic-scale at Tp ≤ 1400 °C. Since CNT confinement could lead to anisotropic crystallite growth in PyCs synthesized below ~1000 °C, and recent modeling indicates that more slender crystallites increase PyC hardness, these results inform fabrication of PyC-based meta-materials with unrivaled specific mechanical properties.
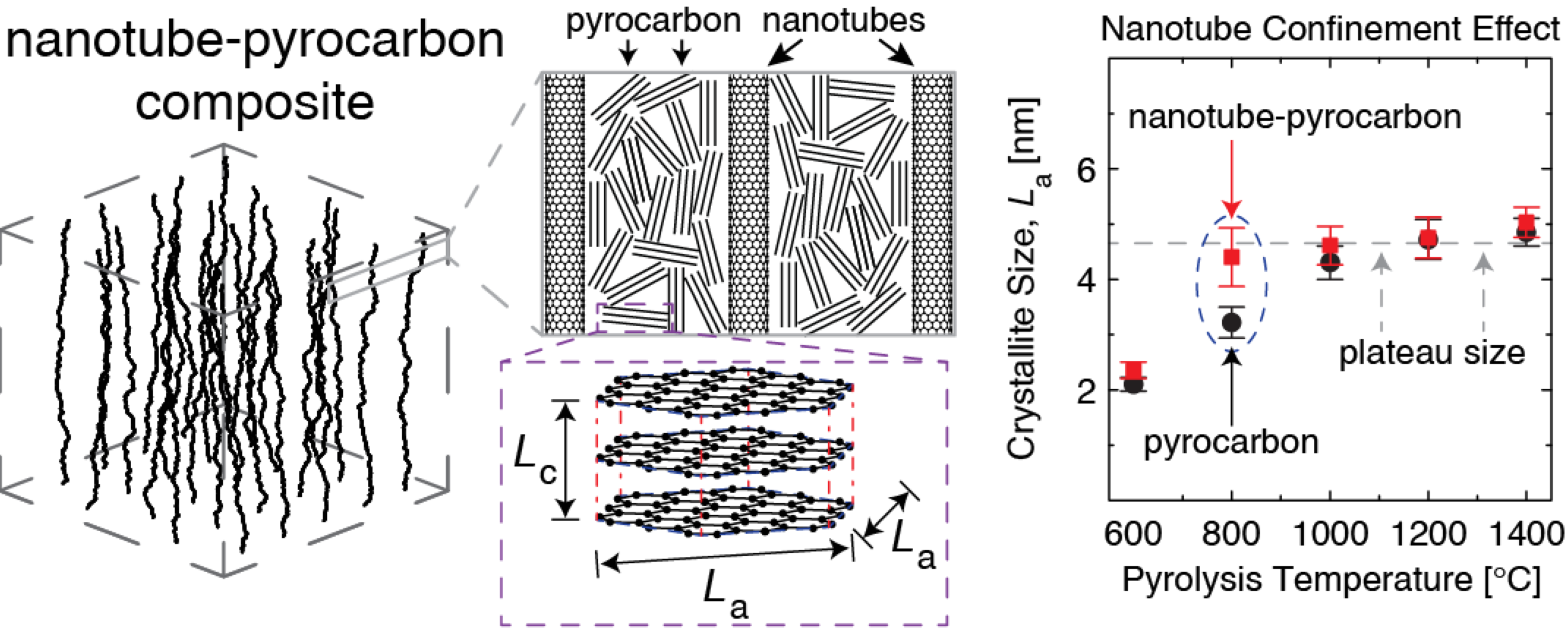
Related Press Releases:
• MIT News: Stronger than Steel: MIT Homepage Spotlight on June 13. (2021)
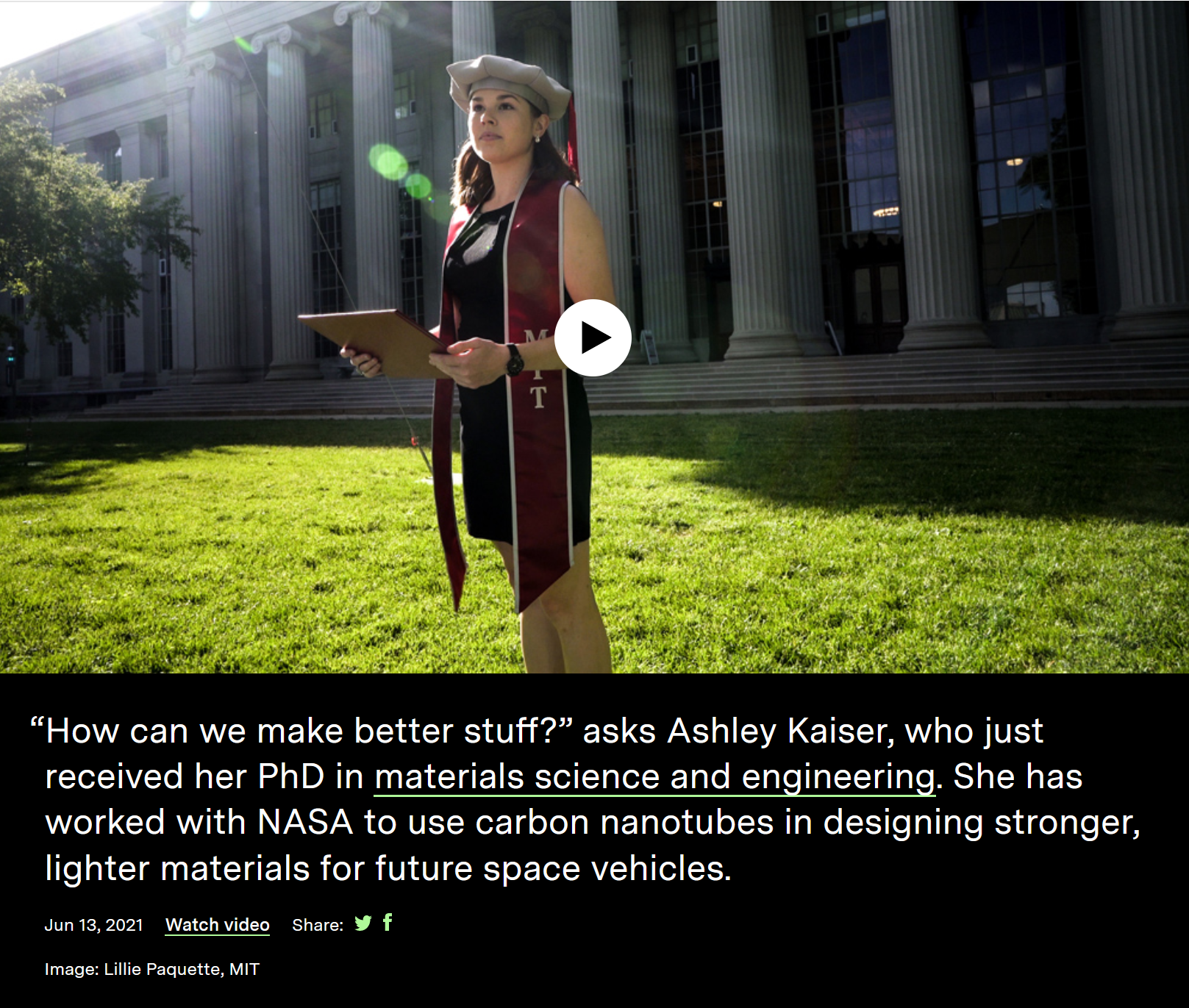
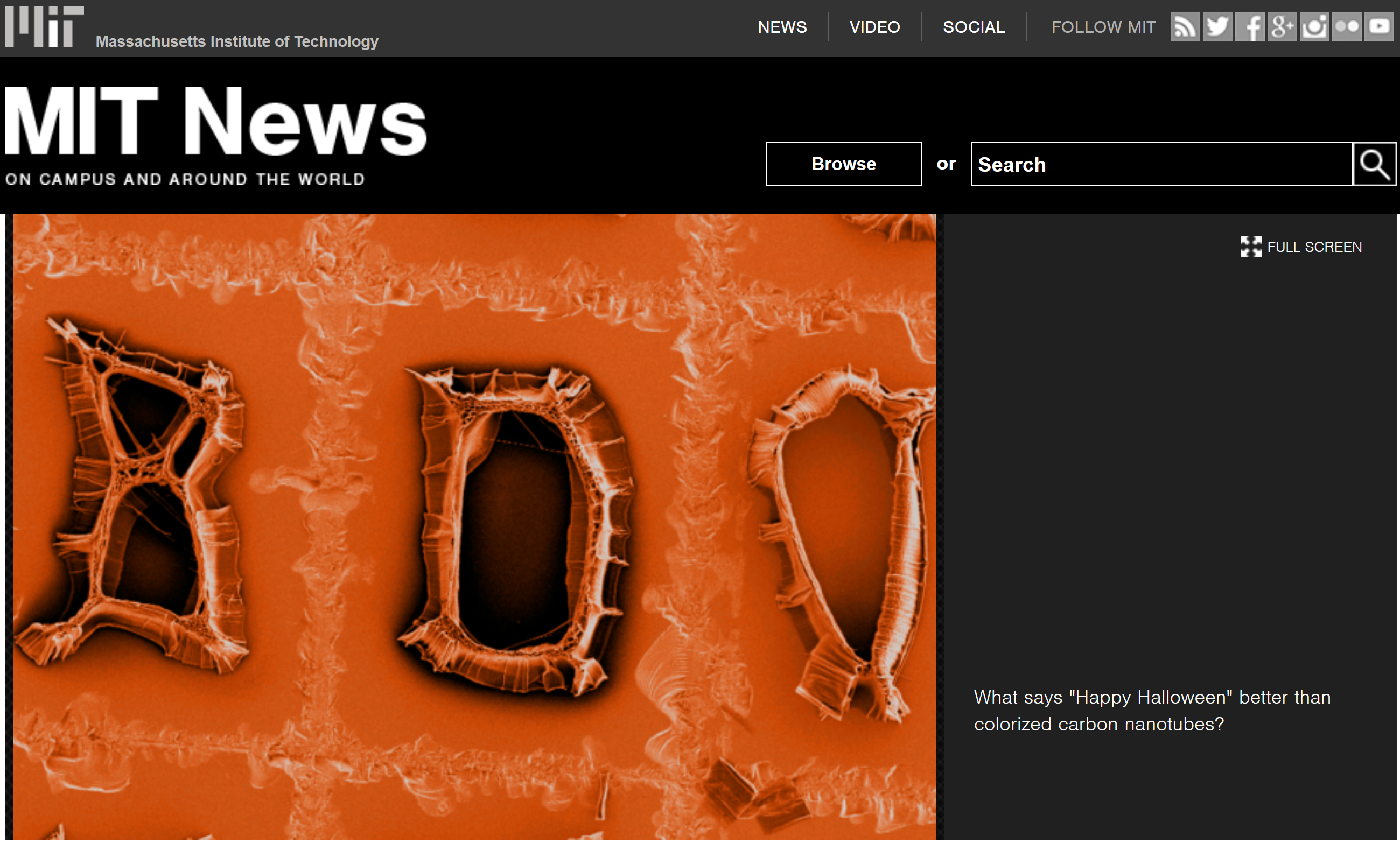
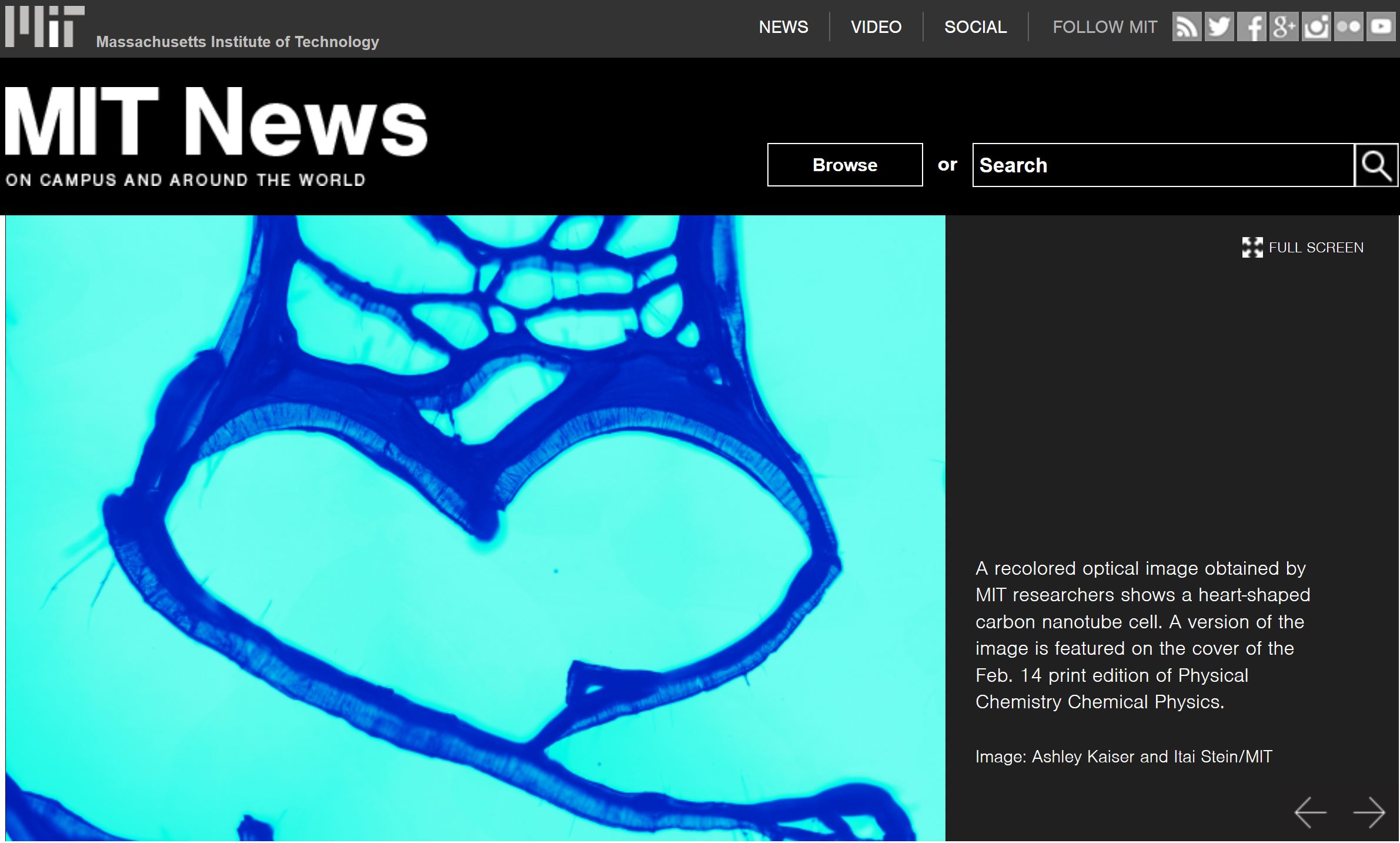
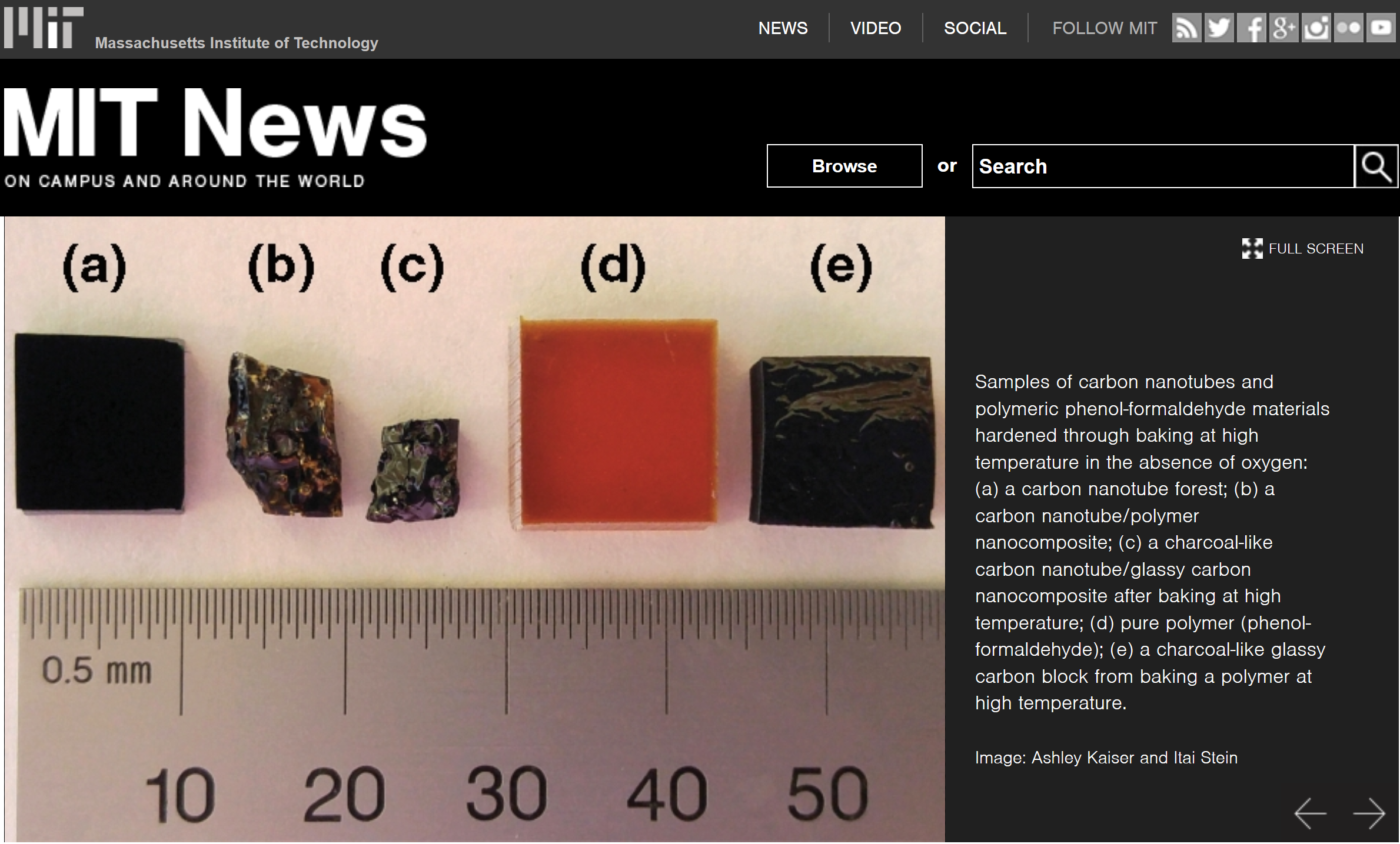
Relevant Publications:
• A. L. Kaiser, L. H. Acauan, A. R. Vanderhout, A. Zaman, D. L. Lidston, I. Y. Stein, and B. L. Wardle, ACS Applied Materials & Interfaces 15, 17029 (2023).
• A. L. Kaiser, A. R. Vanderhout, L. H. Acauan, J. C. Nwenyi, I. Y. Stein, and B. L. Wardle, Carbon 207, 245 (2023).
• A. L. Kaiser, C. A. C. Chazot, L. H. Acauan, I. V. Albelo, J. Lee, J. L. Gair, Jr., A. J. Hart, I. Y. Stein, and B. L. Wardle, ACS Applied Nano Materials 5, 9008 (2022).
• L. H. Acauan, A. L. Kaiser, and B. L. Wardle, Carbon 177, 1 (2021).
• A. L. Kaiser, D. L. Lidston, S. C. Peterson, L. H. Acauan, S. A. Steiner III, R. Guzman de Villoria, A. R. Vanderhout, I. Y. Stein, and B. L. Wardle, Nanoscale 13, 261 (2021).
• A. L. Kaiser, I. Y. Stein, K. Cui, and B. L. Wardle, Nano Futures 3, 011003 (2019).
• A. L. Kaiser, I. Y. Stein, K. Cui, and B. L. Wardle, Physical Chemistry Chemical Physics 20, 3876 (2018).
• I. Y. Stein, A. L. Kaiser, A. J. Constable, L. Acauan, and B. L. Wardle, Journal of Materials Science 52, 13799 (2017).