|
|
|
|
|
|
|
|
|
|
|
|
|
|
|
|
|
|
|
|
|
|
|
|
|
|
|
|
Experimental Geometries
Surface textures
Front-end CAD systems, combined with the geometric flexibility of 3D Printing has the potential for creating some dramatic new geometries. In the parts shown here, a surface texture was defined in CAD and then mapped onto different solids. Such surface textures can be used to enhance heat transfer or create a prescribed surface roughness, for example.
Truss structures
Truss structures of any complexity can be generated and printed by 3DPTM. This feature can be used for thermal isolation (injection molding), or to create a part with prescribed weaknesses (casting). In one application, a ceramic shell was designed with truss structures supporting and surrounding the shell wall. This shell was designed to fail as the poured metal cools, thus eliminating the problem of "hot tears."
|
|
|
|
|
|
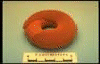 |
|
|
|
|
|
|
|
|
|
3DP part with fine surface feature mapped onto a geometric solid
|
|
|
|
|
|
|
|
|
|
|
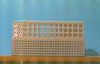 |
|
|
|
|
|
|
|
|
|
|
|
Lattice structures by 3DP
|
|
|
|
|
|
|
|
|
|
|
|
|
|
|
|
|
|
|
|
|
|
|
|
|
|
|
|
|
|
|
|
|
|
|
|
|
|
|
|
|
|
|
|
|
|
|
|
|
|
|
|
Copyright 1989-2000, 3DPTM Laboratory, MIT
|
|
|