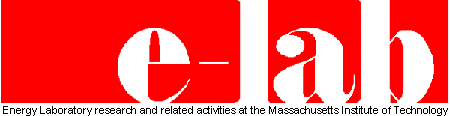
October - December 1998
Straw-Based Insulation for Pakistan: Addressing the Needs of Developing Regions
[Abstract]
[References]
Direct-Injection Automotive Engines: New Insights for Designers
[Abstract]
[References]
SPECIAL REPORT:
Electric Utility Program Refocuses, Disbands
News Items
Publications
[Click here]
[e-lab Home Page]
[Energy Lab Home Page]
[MIT Home Page]
.
n remote, mountainous regions of northern Pakistan, buildings are
typically made of uninsulated stone or cement block. Wood and other fuels
are scarce, and indoor temperatures in winter are frequently only a few
degrees above those outdoors. A straw-based insulation developed by Energy
Laboratory researchers in MIT's Building Technology Program could help
boost those temperatures while saving fuel. Drawing on a technique
developed by ICI Polyurethanes, the researchers place milled straw inside a
tumbler with a central nozzle that sprays fine droplets of an adhesive onto
the tumbling straw. Once coated, the straw is removed, placed in a frame,
and pressed and heated. The straw boards produced can be installed on
interior walls; and they have the insulating value of expanded polystyrene,
the only other rigid insulation available in Pakistan. Half the cost of
polystyrene, the straw insulation could be made in local factories using
local materials, simple machinery, and little energy. Only small amounts of
adhesive would have to be imported. Case studies at four Pakistani schools
show that installing straw insulation could cut energy requirements by half
or more. The methods developed here could be applied in many developing
areas using straw or other available waste materials.
[Read article]
[Up]
.
Direct-Injection Automotive Engines: New Insights for Designers
ew vehicles with direct-injection spark-ignited (DISI) gasoline
engines offer high power and fuel efficiencies fully 30% higher than those
of conventional gasoline engines. The high efficiency of DISI engines stems
from their ability to run "fuel lean," that is, with a lower fuel-to-air
ratio than used in conventional engines. Smooth ignition, however, requires
a relatively "fuel-rich" mixture. The challenge in DISI engines is
therefore to capitalize on the lean part while ensuring a strong fuel-air
mixture at the spark plug. To provide adequate fuel vaporization and
transport to the ignition source, many designs use high-pressure fuel
injectors that provide swirl to the liquid fuel as it enters the combustion
chamber, creating a hollow cone of droplets that stays airborne long enough
to vaporize. However, Energy Laboratory experiments in a transparent test
engine show that the injected fuel may not always form a hollow cone. When
fuel temperatures are high or pressures in the combustion chamber are low,
the hollow cone can become filled in and more jet-like--especially when the
burning mixture contains components with low boiling points, as does
gasoline. The researchers' explanation? When the mixture enters the
combustion chamber, the low-boiling-point components suddenly vaporize with
enough force to shatter the liquid film. The tiny droplets that result are
sucked into the center of the disintegrating hollow cone. The MIT research
findings should help engine designers optimize the geometry of the
combustion chamber to ensure complete vaporization and easy ignition under
all engine conditions.
[Read article] [Up]
[e-lab Home Page]
Last updated: 02/23/1999
Copyright © Massachusetts Institute of Technology
1999. Material in this bulletin may be reproduced if credited to e-lab.
|