Shape - The pressure hull consists of spherical or
cylindrical shapes in various combinations. Table 1 illustrates the advantages and disadvantages of various pressure
hull shapes.
Table 1. Advantages and Disadvantages of Submersible
Pressure Hull Shapes
Shape
|
Advantages
|
Disadvantages
|
Sphere
|
-
Most favorable weight to displacement ratio
-
Thru-hull penetrations easily made
- Stress analyses more accurate and less complex
|
-
Difficult and inefficient interior arrangements
- Large hydrodynamic drag
|
Ellipse
|
-
Moderate weight to displacement ratio
-
More efficient interior arrangements than in sphere
-
Thru-hull penetrations easily incorporated
|
-
Expensive to construct
-
Difficult to perform accurate structural analysis
|
Cylinder
|
-
Inexpensive to construct
-
More efficient interior arrangements than in ellipse
- Low hydrodynamic drag
|
-
Least efficient weight to displacement ratio
- Interior frames required to increase strength
|
Materials
The selection of an appropriate pressure hull material is based on the following criteria:
- Corrosion
Resistance – the ability of a material to resist its deterioration by
chemical or electrochemical action within its environment.
- Resistance
to Stress-Corrosion and Cracking – the ability of a material to resist
failures caused by the combined action of a flaw (e.g. a crack) and tensile
stress.
- Resistance
to Low Cycle Fatigue – the ability of a material to withstand
localized fluctuating stress.
- Creep
Resistance – the ability of a material t withstand permanent
deformation over time.
- Stress
Relief Embrittlement – the process by which localized residual
stresses in a metal are reduced by the reduction in the normal ductility
when a metal is heated to a suitable temperature and slowly cooled.
- Resistance
to Brittle Fractures – the ability of a material to resist failures
with little or no plastic deformation.
- High
Strength to Density Ratio – the material must be strong and light.
- High
Ductility – the ability of a material to deform plastically without
fracturing.
- Fracture
Toughness – the ability of a cracked material to resist catastrophic
propagation of cracks.
- Weldability
– the property of a material which allows it to be welded under normal
conditions.
- Formability
– the ability of a metal to be shaped through plastic deformation.
Submarine pressure hull are usually made of steel, aluminum, titanium, acrylic plastic and glass.
However, the most widely used material is steel, because of a high degree of knowledge available to designers and manufacturers as well as of its
outstanding performance in the ocean.
Aluminum is generally considered unacceptable as a pressure hull material because it is unweldable and is subject to stress-corrosion
cracking. Nevertheless one solution would be to bolt the hull together instead of welding and anodize it to
resist stress-corrosion cracking. Pure titanium is too susceptible to stress-corrosion at high tensile stress levels, but
titanium graphite alloys do not exhibit this problem.
Despite of its weaknesses, such as its brittleness, high sensitivity to
surface abrasion, and considerable strength degradation at joints, glass and
glass-reinforced plastic has a low weight/displacement ratio.
Calculations
For pressure hulls, collapse can occur at wall stress levels below the
elastic limit. This is called elastic buckling or instability failure. Failure
at stress levels above the elastic limit is usually due to plastic yielding of
the material.
The following equations are used to calculate the thickness of each
pressure hull [Sharp, 1981].
- Elastic Buckling Collapse Pressure: The classical elastic
buckling pressure for an ideal sphere
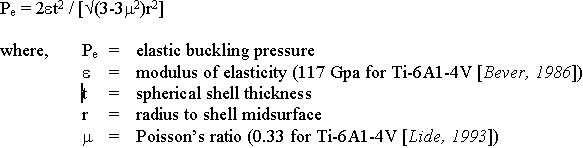
Poisson's ratio is a measure of the simultaneous
change in elongation and in cross-sectional area within the elastic range
during a tensile or compressive test. During a tensile test, the reduction
in cross-sectional area is proportional to the increase in length in the
elastic range by a dimensionless factor, Poisson's ratio [O'Brien, 1996].
The elastic modulus of a material represents the
relative stiffness of the material within the elastic range and can be
determined from a stress-strain curve by calculating the ratio of stress to
strain. Unless indicated otherwise, values were determined in tension [O'Brien,
1996].
According to Arnold G. Sharp, experimental studies have
shown a wide disagreement with the above equation. This is probably due to
imperfections in geometry and material. Extensive recent testing at the
David Taylor Naval Ship Research and Development Center (DTNSRDC) has
indicated that the coefficient 1.22 can be attained in an ideal spherical
shell, but in most cases, even when imperfections are almost immeasurably
small, the coefficient more properly should be about 70% of the theoretical
value. DTNSRDC has recommended that the classical equation be modified for
near-perfect spherical shells to be:

- Inelastic Failure
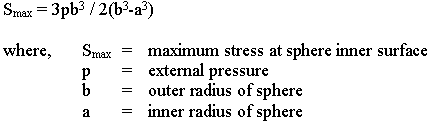
Failure is considered to occur when Smax is equal to the yield strength
of the material (ie. Ti-6A1-4V).
LEEAMITe's Spherical Hulls
LEEAMITe's pressure hulls are designed to withstand pressure at a depth of
5400 m. The operational depth of each pressure hull is approximately 3000 m.
The yield strength of the Titanium Alloy 6A1-4V, the chosen alloy for both
pressure hulls, is 828 MPa (120,000 psi) [Sharp, 1981].
At the depth of 5400 m, the ratio between the wall thickness and outside
diameter is 0.017 [Sharp, 1981].
Passenger Pressure Hull: Inside diameter = 3.00 m
0.017 = x / (3.00 + 2x) , where x is the wall thickness
Therefore, x = 0.053 m Pilot
Pressure Hull: Inside diameter = 1.75 m
0.017 = y / (1.75 + 2y), where y is the wall thickness
Therefore, y = 0.031 m
Volume of Titanium Alloy 6A1-4V in the Passenger Pressure Hull = 1.552 cu.
m
Volume of Titanium Alloy 6A1-4V in the Pilot Pressure Hull = 0.309 cu. m
Density of Titanium Alloy 6A1-4V = 4500 kg/(cu. m)
Mass of Passenger Pressure Hull = 6984 kg
Mass of Pilot Pressure Hull = 1391 kg
Total mass of both pressure hulls: 8375 kg
Cost of Titanium Alloy 6A1-4V and fabrication: $220.00/kg
Estimated cost of both pressure hulls: $1,842,500.00
Exostructure
Outer Shell of LEEAMITe: NS90 - high-strength steel
- C < 0.1%
- Si : 0.15% - 0.40%
- Mn : 0.35% - 0.80%
- P < 0.010%
- S < 0.010%
- Cu < 0.10%
- Ni : 5.00% - 5.50%
- Cr : 0.30% - 0.80%
- Mo : 0.20% - 0.60%
- V : 0.03% - 0.10%
- Yield strength: > 90kg/(sq. mm)
The advantages of this steel alloy are its great strength and high corrosion
resistance. Although it is rather heavy heavy, the outer shell is not required
to be thick. In fact, the exostructure does not have to withstand enormous
amounts of pressure because the empty spaces within are filled with mineral oil.
Certain types of mineral oil have comparable density to sea water and the
substance is an electric insulator, which protects the electric connectors and
equipment.
References